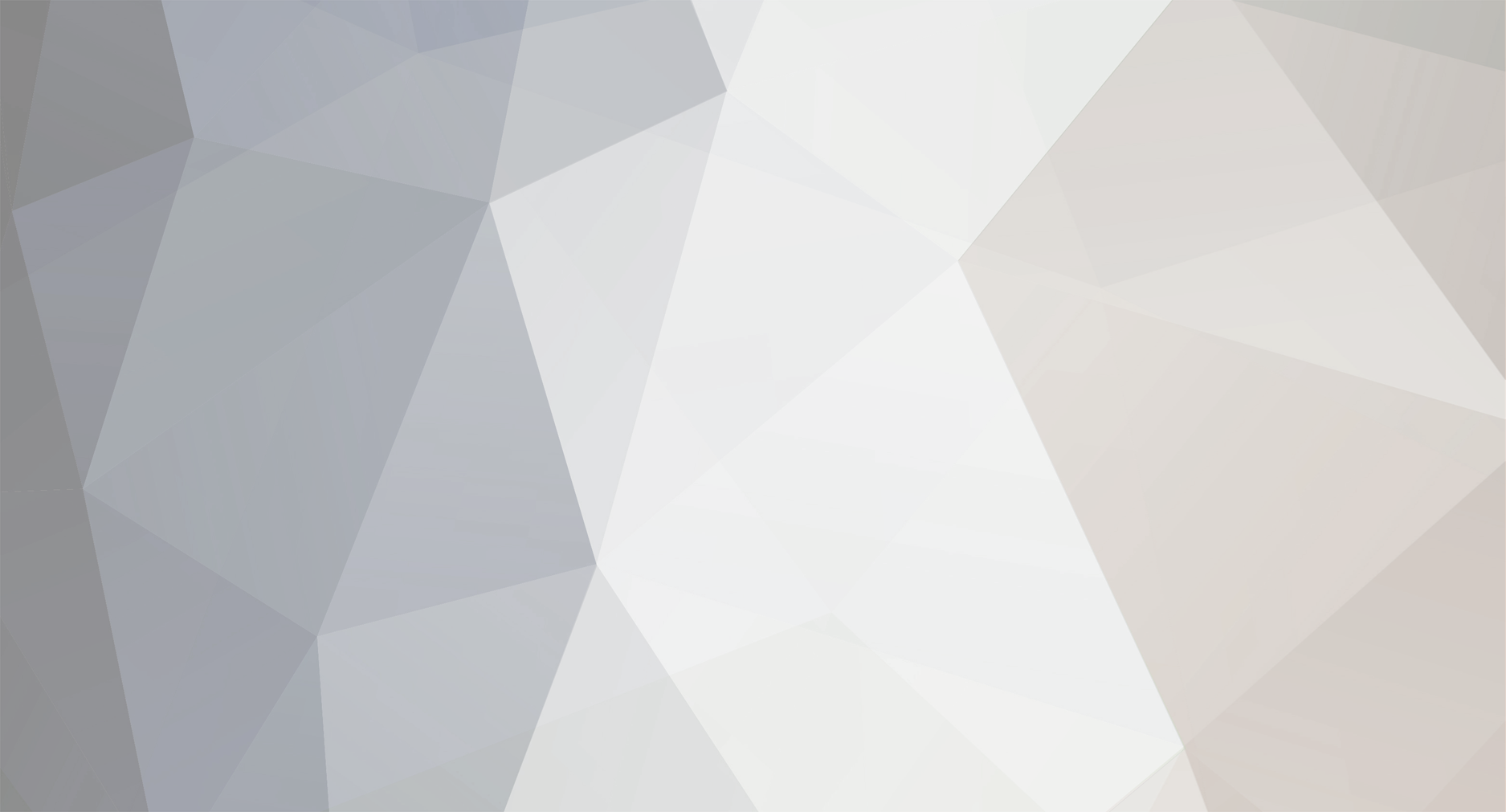
JuhaV
Members-
Posts
99 -
Joined
-
Last visited
Profile Information
-
My bike(s)
Used to have Sport Corsa 1100i 1999, now driving Honda VTR SP1
JuhaV's Achievements

Guzzisti (2/5)
0
Reputation
-
Using the barometric ECU input for the lambda feedback might work just fine !!! Pressure indicates air density in the airbox. Increasing air density requires more fuel and vice versa. This relationship should be linear, as with increasing pressure the amount oxygen available for combustion increases at the same rate. So, programming the lambda controller to match the barometric pressure sensor voltage would to the trick most likely. Because lambda will indicate whether there is enough or excess oxygen for combustion, one might even completely dump the pressure sensor. Hmm, Honda has also a MAP sensor (Manifold Air Pressure) ... Seems that with clever programming of the wideband lambda controller one could try quite many kind of approaches to "misuse" any of the ECU inputs that will affect fule injection. Hope that I had more free time to experiment with these things. br, JuhaV
-
dlaing, That is a very interesting idea ! To substitute the temp sensor output with the lambda generated voltage. Yes, that can work just fine if the ECU will use the temp sensor output in some substantially linear manner to rich or lean the mixture. In an aircooled Guzzi with just one temp sensor this is most likely the case. The lambda sensor controller could be programmed to "match" that effect. If the mixture is too lean, the temp sensor input to ECU would be fooled to indicate that weather is colder and vice versa. However, I will try to apply this to a HRC Honda, that has quite a bit more complicated FI system and several temp sensors in various places. I have no idea whether any of these would affect the mixture in a linear manner. I do know that in a case when the cooling water temp is rising above certain level, ECU enrichens the mixture to help to cool down the engine. Forward and rear cylinders have different fuel and ignition maps etc. Thus the mixture that ECU chooses to inject depends on several sensors. Might be that one of the sensor inputs could be used for that but that would need more studies. As I already have the Powercommander USB and wideband lambda, I am only trying to find a proper reason to buy the new gadget, the very technical and nice looking LCD unit br, JuhaV PS. Tuneboy info and pics would be nice. We might get some new ideas ...
-
Phil, pictures would be nice, especially when the unit is on the bike to get better idea of the size/visibility. My bike is most of the time for track duty only so the weatherproofness is not a big issue. It also normally stays inside during nights and for the time it being outside, the LCD unit needs to come out so it will not be stolen. The gist here is that with the more and more restrictive dB-limits at the tracks, I need to use dB-killers at some tracks and no dB-killers at some other tracks. It would be so nice if the bike would "automatically" compensate in the fuel injection for these changes to always provide optimal AFR. I was thinking more of the possible issue that if the lambda voltage signal fluctuates in some occasions wildly and if the LCD unit tries to trim the fuel injection without any damping these fast changes, the most straightforward solution would be to arrange an electronic (active or passive) low-pass filter to the 0-5 V signal line between the lambda unit and the HUB/LCD. There it is possible to select a response time for the filter to average the signal mildly to make it more stable. This is basic electronics and can be done at a cost of a few euros. This is becoming interesting, looks like it needs to tested in practise br, JuhaV
-
Phil, You are correct, the Powercommander will not accept any sensor inputs, however, the LCD unit equipped with the HUB will do so. In principle,what is needed would be 1) Disconnect original lambda from the ECU (Honda RC51 nor MG Sport 1100i does not have one so we can skip this) 2) Plug LCD unit to Powercommander 3) Plug HUB to LCD to provide "pressure sensor" voltage input to be used now as our lambda voltage input 4) Install wideband lambda sensor and connect the 0-5 V output to "pressure sensor" input via HUB to LCD 5) Program wideband lambda sensor controller to provide suitable AFR to voltage conversion, for example, 0 V = AFR 12 and 5 V = AFR 14 6) Program LCD to trim fuel injection based on the "pressure sensor" input voltage. According to Powercommander manuals, the HUB will provide 0.25 V resolution for the 0-5 V signal, so between AFR 12 and AFR 14, according to the example above, we could have 20 trim values. 7) Go and ride. Raz, thanks for the welcome ! I will need to do some testing with the wideband lambda unit that I have (Australian 2CO) to see how the 0-5 V output behaves during warmup and so. And how easy it will be in practise to reprogram the AFR to voltage conversion in it. Then, if that part goes well, I perhaps need to go and buy the LCD + HUB. Powercommander does not specify how many times per second the pressure sensor input is read, but I think that it is likely that it will be fast enough, perhaps once per each injection cycle. Even something like 10 Hz would be ok because the response rate of the lambda sensor is not much faster. The trim values keyed in the LCD can be limited to max. plus minus 15-20 % from the base map values, so the base map needs to be good enough that is easily achievable. Phil, according to the LCD unit manual the unit provides only the LOW, MID, HIGH fuel trims (basically the same as with the buttons in the Powercommander unit) so as you said, an additional Palm or laptop is needed to really edit the trim tables. As you Phil have the LCD unit, perhaps you could comment whether the LCD display is bright enough to be visible in direct sunlight ? If so, and weatherproof enough, I could consider removing the original speed and rpm display unit from my bike and replacing it with this cool LCD display instead br, JuhaV
-
Hi, After having sold my Sport Corsa 1100i, I have not been writing to this forum lately, but remembering that here are people that have considered lamda sensors, ECUs and especially Cliff's remarkable My16M and My15M units in depth, I decided to ask your opinion regarding the following. Please see the threat here. Sorry, that is a Honda RC51 forum but I am driving one of those nowadays The key of the question that I have tried to present on that forum is whether it would be possible to "misuse" the pressure sensor input of the Powercommander LCD unit to trim the fuel injection in real time based on wideband lambda sensor output ? Any comments regarding this would be welcome. br, JuhaV PS. I had a My16M in my Sport Corsa together with wideband lambda and closed loop feedback to trim AFR. It worked out very well.
-
These are custom made one-off's as on my previous bike. Designed to give some real protection. Thick aluminum plate covered with black plastic sliders. Design by Kari. http://www.kolumbus.fi/koivupiha/hw2005/sideview.JPG Always wondered why these type of sliders are not available commercially ... br, JuhaV
-
Hello Nigel, I found your pressure gauge project very interesting and was bondering same type of instrument when I had a Sport Corsa. However, nowadays when driving a Honda VTR SP1 the need for balancing throttle bodies seems to have almost completely vanished A few years ago I developed my mental design for the pressure gauge up to the following stage. I try to shortly describe it here in case it would be helpfull to you. The basic idea was to use a differential pressure sensor that would be capable of measuring pressure difference between two inputs. There are such sensors available but the pressure range at least for the economical ones is rather limited. Now, as you know if you plug the inputs directly to the left and right inlet manifolds, the pressure pulses are much too strong. However, if you would plug a pressure line into the inlet manifold, then add a restrictor into the line followed by a somewhat larger volume chamber, the pressure changes in that chamber due to the restrictor are damped down. If the size of the restrictor jet is made smaller at some point the pressure in the chamber stabilizes (becomes averaged) very effectively. The downside of this is of course the fact that the response time for the chamber pressure to follow the inlet manifold pressure increases. In practise I found that very good restrictor jets can be manufactured from medical syringe needles that are available in different gauges. Just go to the pharmacy and buy a set of those needles in different sizes. Using two identical ones provides two restrictors that are identical to a very high degree. The chamber after the restrictor needs only be about a few cubic centimeters in volume. The ratio of the chamber volume compared to the aperture size of the restrictor jet defines the damping effect. I simply used plastic fuel filters to provide those necessary chamber volumes (the transparent ones that you plug into the fuel lines). A line (silicon tubing) from the inlet manifold was plugged into the filter inlet so that the syringe needle was first pushed into that same filter inlet remaining thus inside that silicon tubing. Now considerer having each inlet manifold equipped with a pressure line, restrictor in that line and following with a stabilizing (averaging) chamber. Then plug the inlets of a differential pressure sensor into these chambers. What kind of signal would you see on the sensor's electrical output ? I suppose (not tested this in practise) that it would be slightly pulsing signal showing the left-right variation in the restrictor damped inlet pressure pulses. If you now add electrical low-pass filtering (= averaging) to that signal, there you are with the wanted pressure difference ! I suppose that the system could be damped & averaged down to the degree that it only needs to have a response time of a few seconds. That is fast enough for the system to be usable for adjustments. What do you think ? br, JuhaV
-
http://www.dieselmotorcycle.co.uk/ The last link in the left column has a short video when you scroll down past the pictures on that page. br, JuhaV
-
Hi Alex, Some answers to your questions : 1. http://www.tlm.nl/magazijn/webshop/detail.html?aid=10943 You need to do your own painting design & job, because the glassfiber cowl comes with primer only. 2. The pods were RU-1780 equipped with red RU-0510PR "PreChargers". They worked really well I think. Good power and very very nice sound. I did not notice any ill effects whatsoever. The PreChargers are especially nice if driving in rain. 3. I did not get it to Dyno, but it sure did run nicely and was much more eager to rev than before those mods. I would think that it was around 100 hp from the crank. 4. Tech Edge : 0 258 007 057 LSU sensor + 2C0 unit + LD02 display 5. Yep, quite a bit of work was done, but the bike was at that point "ready" and I needed something new to tinker around. The new project is here : http://www.kolumbus.fi/koivupiha/sp1.htm The new one does not have as much soul as the Corsa had, but it does corner like a surgeons knife br, JuhaV
-
Alex, With my Corsa steady 90 km/h would produce as low 4.5 l/100 km consumption (My16M & closed loop mode). Normal riding 5.5-6.0 l/100 km. At track 10 l/100 km could be achieved without any problem. The symptoms of your bike sound that you might have either the cylinder head or outside air temperature sensor gone wacko. This can enrichen the mixture up to 30-50 % ? Because it sounds that the bike otherwise runs ok I would go checking those sensors first. br, JuhaV PS. By the way, my current ride is a slightly modified VTR SP-1
-
Sorry but nope, they are now on another Guzzi. I sold the Corsa with the original crash protectors. Only one set of those special sliders were manufactured. The new Corsa owner would have needed them thought, because he crashed that bike on a race track after owning it only less than two weeks br. JuhaV
-
Hi, For an alternative slider design please take a look here : http://www.kolumbus.fi/koivupiha/hw2005/sideview.JPG http://www.kolumbus.fi/koivupiha/hw2005/behind.JPG Those were made for my Corsa by a friend of mine. The aluminium part is 10 mm thick and the plastic was black Delrin or something similar. I ain´t riding a Guzzi anymore but peaked in here and thought that you might be interested to see those sliders. Happy Christmas everyone ! br, JuhaV
-
The valve stems and guides in my Sport 1100i were gone at 33000 km just the way it have been described above. I suspect that the soft materials of those together with somewhat aggressive cams make both Sportis and V11s prone to this problem. I believe that Stones and Californias with smaller valves and less aggressive cams might not have that problem even if the material hardness would be the same ? Interestingly, the wear of the stems was not evident at all before I pulled of the head and detached the valves. My repair was K-lining and new valves from Mike Rich. I considered the change of the complete guides excessively brutal. K-lining should work ok and can be repeated if necessary. br, JuhaV
-
Hi Göran, Looks very good ! Those FBF pistons have pretty different top shape compared to Mike Rich pistons, but on the other hand those FBFs are closer to the tradional high comp Le Mans pistons. Can you remember how thick are the pistons rings ? Are they thinner than the original ones ? I have been driving now about 1000 kms with my new set up and I am pleased with the results. The engine revs up very effortlessly and seems to have some additional punch in the mid and upper ranges. Just yesterday I finalized the electronics by connecting a Tech Edge wideband probe to the system. Now wideband probe gives feedback to the ECU and thanks to Cliff's recent developments I can give different lambda targets to different parts of the map. I tested this yesterday only for about 100 kms but it works beautifully. I will try to update my www-site soon with pictures. br, JuhaV http://www.kolumbus.fi/koivupiha/hw2005.htm PS. I will be going to Virtasalmi Motopark track for some "testing" in the weekend after the next one
-
Effective = lets fewer particles through, ok, but also reduces airflow and therefore restricts power. I think that those numerous dyno runs show that open airbox + K&N or those oily pods can give more power in a guzzi if at the same time more fuel is added to keep the AFR correct. Safer = longer engine life. Yes, but in motorcycles if you change your oil every 4000-5000 kms, how big is this effect ? In a diesel truck driven on dirty roads 500000 km this is surely important. How about in a motorcycle driven on good tarmac 50000 kms mostly in reasonable weather ? Cheaper = less money. Yes, but many of us do not count the value of motorcycling in dollars per kilometer It would be cheaper and safer to drive a diesel truck. It is very difficult to estimate what the effect of the air filter properties on engine life really is. I suppose that when driven in normal circumstances on tarmac the use of K&N or corresponding filters is not the limiting factor. In the old days, many bikes did not have any kind of air filter. A grid to prevent stones entering the inlet was all they had. However, I could be wrong here but at least for me, this risk is clearly compensated by those few extra ponies, nice inlet roar and sportier look of the bike br, JuhaV