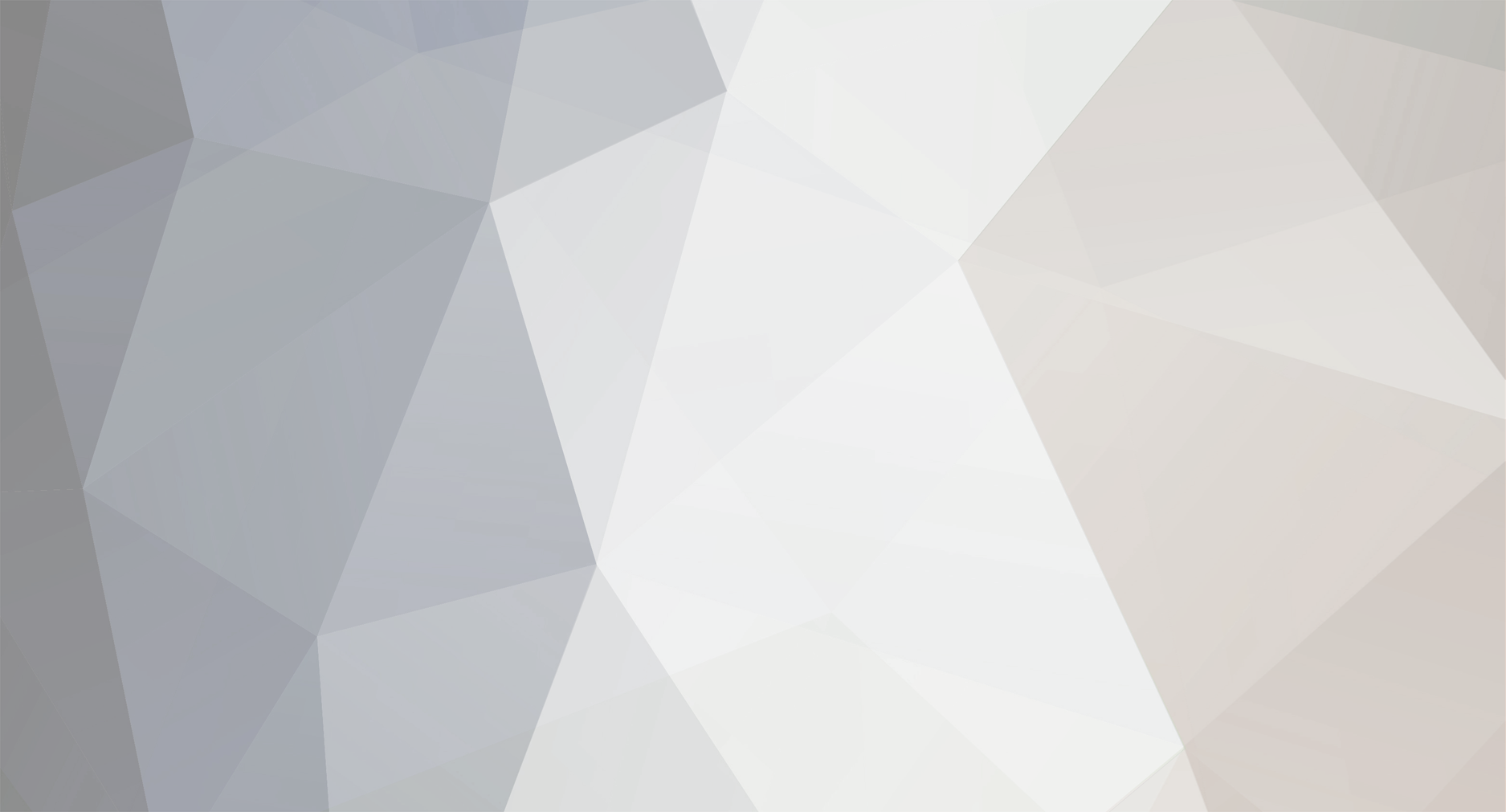
moto
Members-
Posts
133 -
Joined
-
Last visited
Profile Information
-
My bike(s)
none
Recent Profile Visitors
The recent visitors block is disabled and is not being shown to other users.
moto's Achievements

Guzzisti (2/5)
0
Reputation
-
In http://www.megasquirt.info/PWC/LSU4.htm it says: "For the rich mixture side, where there is no oxygen, the sensor measures the amount of CO and H2 in the exhaust gas" The way the rest of the text reads, they are trying to keep the cell at 14.7:1 and the oxygen is either pumped away or provided by reaction and pumped in to make this happen. What convinces me that the oxygen must be gone completely for the thing to react CO and H2 is that I don't think the thing can pump oxygen out and in simultaneously. Maybe not all of the O2 on the rich side is provided by reaction? They also say this: "We have explained the excess-oxygen case where the air-fuel mixture is lean. How does it operate on the oxygen-depleted side, or rich air/fuel ratio side? For this case, oxygen is ‘pumped’ into the measurement cavity simply by reverse application of current on the pump element. Feedback on the Nernst measurement cell indicates when stoichiometric equilibrium has been achieved. Now, something should be bothering your gut right about now…The pump cell operates on oxygen ion transport, but we are in a situation where there is no oxygen in the air-fuel mixture (i.e. we are rich). If we become much more rich, we still do not have oxygen. Super rich, and still no oxygen. How can there be a feedback situation in this case?" To me, this quote implies that they expect all O2 to be gone when the thing goes from pumping out to pumping in (i.e. on the rich side of 14.7:1). The word "stoichiometric" (which for gasoline is 14.7:1) also implies that all oxygen (and fuel) is used up. Since this is not possible, it would be of some (limited) interest to know just how many percent O2 they expect to be left over at 14.7:1, if not zero. This then brings up that the sensor could only be accurate for one particular level of efficiency, if at all. Regards, Derek
-
Right, but this is when no oxygen is left over whatsoever, and an engine will rich misfire before no oxygen is left (remember 0.2% O2 with a CO of 12.6%). At that point of course there will be a whole bunch of oxygen left over, which will prompt the ECU/autotuning software/Wideband Commander/tuner who is not paying attention to add even more fuel. Regards, Derek
-
You can record all of the stuff with the VDSTS untill the cows come home, and the limitations of using an O2 sensor and the fact that you cannot measure horsepower and cannot put a steady load on the engine will prevent you from getting results as good as possible on a proper dyno. Once again, I can test any and all throttle position/rpm combinations one would ever encounter on the street (and some one would never) with step testing. The rate of throttle opening makes very little difference on an injected engine. Think of it this way: At any given time there will be a certain MAP, TP and rpm. If you tune for all of them to be correct, it does not matter at what rate the ECU is moving around between cells. Certainly, you will not be able to get useful information from an O2 sensor under the transient conditions of a moving throttle. I think we might, as I sometimes have trouble following you, and you sometimes have a hard time following me. Certainly, we would have to repeat ourselves a lot less if we didn't. These folks and I are in agreement on all points. I never said that I didn't think temperture had an effect on anything. What I did say is that for me to maintain temperatures accurately is not a problem. I am able see changes that result in as little as .1 to .2 hp on my dyno. This would simply not be possible if the temps were not controlled closely enough. Let's start from the beginning: Under perfect conditions (i.e. 100% efficiency), there is some amount of oxygen required to burn a known quantity of fuel with no leftovers. Unfortunately, 100% efficiency only occurs under the controlled conditions of a laboratory experiment. There must then be some "average" combustion engine efficiency that is used to calculate "A/F ratio" from oxygen content. So, we've arrived at the first problem: There is no direct correspondence between oxygen (or any other gas) content and "A/F ratio". Second, the ideal "A/F ratio" varies from engine to engine and from one rpm/throttle position/load combination to another. Imagine we equip a vehicle with a fuel flow meter and a mass airflow sensor. We then add or subtract fuel so that we have a stoichiometric mixture (as evidenced by the fuel flow and air mass measurements) at a particular chosen throttle position/rpm. We then screw a wideband "lambda sensor" into the exhaust. Do you think it will show a lambda value of 1.0? We then tailor the amount of fuel to yield some desired BSFC or HP. Do you think the A/F ratio as measured by our fuel flow meter/mass air flow sensor combo and our "lambda sensor" will match, or even be offset by the same amount? Say we try this experiment at a different throttle position/rpm. Do you think the results will match, or the offset from the previous comparison will be predictable, and therefore transferable to other throttle positions/rpm? Say we map this all out so that we know what these values are at all throttle positions/rpm. Will it carry over to another engine of the same model? And what if there have been modifications? Third, I'd like to consider what the goal of tuning is in the first place. Is it to get a particular "A/F ratio"? It's more likely that we would like the engine to make horsepower and be efficient (i.e. get good mileage). Looking at oxygen content has limited use when trying to achieve these ends. However, don't get me wrong, oxygen measurements are actually good for something. Once you have tuned for max power by adding and subtracting fuel, the oxygen numbers can help you to detect a retarded ignition timing, misfire, or stagger issue (all of these produce an excess of O2). If you go straight to a particular oxygen content, you completely ignore these factors. Even once you've corrected these, the oxygen content can still vary substantially (somewhere between .1% to 4%). So it can often help to point you in the right direction, but isn't the final arbiter of anything. CO on the other hand can, once a proper value has been established through bracketing, be used throughout as a target to set the mixture strength close to optimum for power and mileage. CO is also not the final arbiter of anything, but it tells you much, much more about whether an engines map is in the ballpark than O2. You can hit an oxygen target right off the bat while the engine has the completely wrong amount of fuel, a misfire and/or wrong timing, whereas with CO, fuel will be close, guaranteed. As an example, there are spots on two Aprilia Futura dyno charts I have, where the O2 content is 0.2%. One has a CO of 12.6% (this is drowning rich!) and the other has a CO of 3.2% (perfect at this particular throttle position/rpm combination). With 3 to 5% CO being a good range for most motorcycle engines, I'm sure you can draw your own conclusions from this example. Then there are all of the sensor/controller related issues, such as that abrupt changes in probe temperature (on off throttle transitions for instance), minute changes in voltage/voltage offset (turning lights/accessories on and off, changes in charging voltage due to rpm), and changes in exhaust pressure (again on off throttle transitions for instance), will cause inaccurate readings. There has been some work done to minimize these and other errors with sophisticated controller technology and careful calibration/setup. See http://www.bgsoflex.com/pwb/0.95/PWBV0.95_QandA.pdf and http://www.techedge.com.au/vehicle/wbo2/wblambda.htm. I think very few if any readily available WBO2 sensor/controller combos manage all of these factors effectively, and even if they did, that still leaves the inherent unsuitability of O2 by itself for determining suitable mixture strength. Then there are the delay problems, which will vary fairly unpredictably, or else one could just build an appropriate time offset into the controller, logger or ECU. These delay problems mean that an O2 sensor can only really be used to tweak a map at steady throttle and rpm. Unfortunately, this also means that it can't be used when the engine is really making power (unless you are going up hill with a head-wind). So-called closed loop ECUs either only tweak a setting after the engine has been at steady state for a while, confine inputs from an O2 sensor to a narrow band of rpm/throttle positions, or both. Most ECUs that use O2 sensors do so not to keep the engine running at peak efficiency, but to keep a cat functioning properly. If you insist on trying to use an O2 sensor for tuning, you still need to come up with proper sensor target voltages. These targets would be developed by seeing what values exist at peak HP or best BSFC at each breakpoint. But by then, you already have a perfect open loop map that stands to be harmed more than helped by O2 sensor inputs. I've heard people argue that you can use an O2 sensor to build a map that is in the ballpark when you are starting from scratch. Even that is not possible, as the ECU will get similar input regardless of whether an excess of O2 is due to too little fuel or due to too much. Further recommended reading: Motorcycle Fuel Injection Handbook http://www.factorypro.com/dyno/4gasEGAvso2sensor.html Certainly, the cat will change the readings (after all that's what it's designed to do), and on vehicles equipped with them I install a bung ahead of the cat to take readings from. Why would measuring at the exhaust end be "a great mistake" on non cat equipped engines? Are you thinking that reversion would introduce outside air? If so, not to worry, as I use a probe that sticks up to 30" (760mm) into the exhaust. Again, how can not allowing the engine to accelerate at all fail to be enough resistance? How can maintaining the engine precisely at whatever temperature you like not be good enough? Now you are really confusing me. You say that a dyno is not good enough for you, and then say that yours and others subjective opinions are. That seems totally backwards to me. Regards, Derek
-
OK, so what measurements are we talking about then? It's just another way of saying that just because a certain number of people believe something doesn't make that true, and that just because a certain number of people do something doesn't mean you have to do it too. I thought you were saying that the cylinder head or oil temperatures encountered while riding around would not be as low while on the dyno, because there is not likely to be sufficient air speed over the bike. I was pointing out how this is not necessarily a factor when step testing, and why. I think we may have a language barrier here, as now I'm having trouble following. What I am saying is that I consider O2 sensor derived AFR to be essentially useless, no matter if monitored on the street or on the dyno. I have not yet seen any measurable differences in exhaust gas content from one temp to another on a injected bike. I think I have either not tested across a broad enough range in terms of conditions, or simply gotten lucky in that the existing corrections were actually pretty good. Unfortunately, the results achievable on a brake dyno with 4- or 5 gas EGA will be essentailly impossible to duplicate on the street with O2 sensor derived AFR. Regards, Derek
-
With my dyno in step test mode, the engine is held at a constant rpm and not allowed to accelerate at all. This could be because cells adjacent to each other may not all be tuned correctly, and because of the inherent limitations of an O2 sensor. Agreed. Higher resolution is better. Put the thing on a brake dyno with a 4 or 5 gas EGA. Technically, this is synonymous with "mediator". In this context one could substitute "determiner". If a bunch of peple jumped off a cliff, would you? Certainly, but there are more and less effective approaches. Agreed, except in most cases the dyno is a more accurate instrument than perception. With step testing, the airspeed only needs to be enough to allow a step to be initiated and ended with a reasonable and repeatable beginning and ending engine temp. In my opinion, you would have to independently control oil and air temp on a brake dyno with 4- or 5 gas EGA to properly tune the compensation tables. Regards, Derek
-
There is absolutely no reason why an engine should not run right when it comes off the dyno, unless it was tuned to an "AF ratio" instead of to best power, BSFC, or even a CO between 3 and 5%, or unless certain breakpoints were neglected. Regards, Derek
-
Not this again... My dyno creates whatever load is necessary to to hold an engine at whatever rpm in whatever gear and at whatever throttle position I choose. Certainly, Mr./Ms. Desdinova's tweaks would show up on my dyno. What is to prevent somone from testing various throttle openings on the dyno? This is incorrect as the map is a grid with throttle positions or manifold air pressure along one axis and rpm along the other. The rate of opening is relatively inconsequential on an injected engine, as the engine is not relying on engine vacuum to supply fuel. There are certainly not 30 or more different maps. On an ECU with both TP and MAP tables, there could be over 30 rows per cylinder to tune. Could this be what you mean? That sounds reasonable in most cases. However on some engines, depending on the state of tune, best power everywhere will make the bike difficult to ride as the HP may increase by 20 hp over the span of 1000 rpm (as an example). Actually, if you want best power, it is best to stay away from supposed AFR measurements, at least by O2 sensor. If you want best power, power, rather that O2 content, must be the arbiter. In fact, looking at AFR as derived from an O2 sensor can mislead severely. You will be best off with going with what you notice, regardless of the values returned by an O2 sensor. Agreed on all points. Regards, Derek
-
Note the "crankshaft din" business. The engine was tested on an engine dyno (rather than a chassis dyno) or a dyno that measures the driveline losses, or some silly arbitrary "correction factor" was applied. Regards, Derek
-
What would help your argument would be to ask for the comparisons for all of the other throttle positions including EGA data. Regards, Derek
-
I think there is a chance a pre-fab map can be correct, but my experience corroberates that the chances are slim. Considering how many breakpoints there generally are in a map (multiplied times the number of cylinders), and in the case of Guzzi, temp & pressure correction problems, there are many chances for errors. I have to wonder where the 100 people you spoke with took their bikes. Regards, Derek
-
Realizing that this post was mostly in fun, I still have to say that faith based tuning is precisely what I am against. Don't you want to know that the engine is running a particular way rather than believing it? While I understand and agree that there are no absolutes, it is possible to proceed based on evidence rather than faith. Gathering the evidence requires the equipment most suitable to the task. Would you go have some tea leaves read in order to determine the state of tune of your engine? To each his own, but I don't see it as likely, nor likely to be accurate (you never know I guess). Likewise, you are not likely to have your local shamanic practitioner perform some ritual to to get your engine to run better (unless the "ritual" involves brake dynos, EGAs and maybe flow meters). People do seem to get nearly as defensive about their faith based choices with regards to tuning as they do about their choice in religions (so far, short of killing each other). Regards, Derek
-
Hmm, I'm not sure how you could ever get the map to ping, although the engine might... Two of them with logging might. I would love to do it. Does anyone want to let me borrow the equipment? It must be noted that this comparison will not demonstrate the problems related to input voltage, probe temperature, pressure variations or transient response, as in order for the EGA to work, testing must be done steady state. The way to include those problems in a comparison would be to "Autotune" (with PC or TuneBoy), let an ECU (such as Cliffs) tune itself in closed loop mode, or manually tune using a WBO2 sensor and then see by how much I could improve the mapping from there. Regards, Derek
-
I'm sorry, but I don't smoke. I had not read post #57 before my last post. I was referring to post #1, where you said "You will note that there was no huge gain in HP or torque, but it flattened the A/F curve nicely. which should result in notably better milage becasue the curve was WAY rich above even best-power." I read post #57 just now, and I consider whether or not you will achieve the results you are after with this method to be debatable (see the ECU thread if you have not already). Regards, Derek
-
Right, but what I'm getting at is that 100% throttle runs say very little (if anything) about what to expect in terms of mileage. Derek
-
Hmm. Then I'm confused about the claim of improved milage in your original post. Regards, Derek