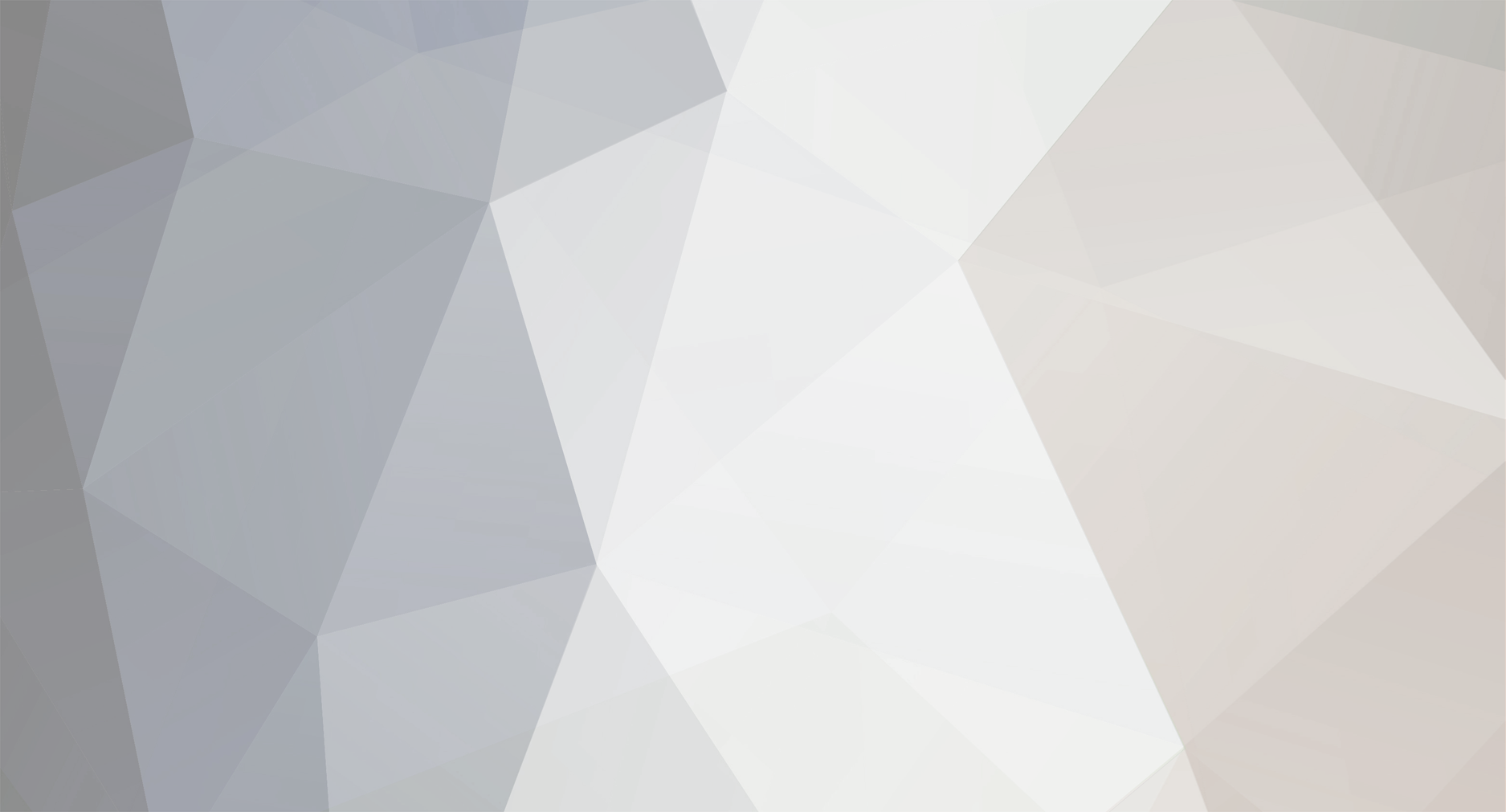
Ryland3210
Members-
Posts
1,033 -
Joined
-
Last visited
-
Days Won
1
Content Type
Profiles
Forums
Events
Gallery
Community Map
Everything posted by Ryland3210
-
Welcome to the forum! You'll find there is a wealth of technical support from dedicated members. My guess is that it isn't necessarily the relay, but the socket it plugs into or the wiring to that socket. Pull the relays out and take a close look at the terminals in the socket. Maybe they have lost their spring loading against the relay contact. If they have gotten hot due to intermittent or high resistance contact, the metal may have gotten soft. You could work with a scribe or thin screwdriver to attempt to bend them so that they grip the relay contact better. If it looks like that's not the problem, take the socket out and have a look at the wire connections to the terminal. If all else fails, and at the risk of sounding like an advertisement, the relays I offer from Omron do have thicker terminals made of copper which make better contact with the socket.
-
At 3000 RPM, three quarter open throttle, think of it this way: The RPM and throttle position determine the torque the engine puts out, all other things being constant, so the load on the bike determines how long it stays at that RPM. If on an an uphill grade, it will accelerate slower than on a downhill. As long as it stays at that RPM, the intake manifold absolute pressure will remain the same. Whether you are in one gear or another has no effect on manifold pressure. It will only affect the bike's rate of acceleration/deceleration. Of course, that will change RPM. To say it another way: the engine is a fixed displacement vacuum pump as far as its suction of the air/fuel mixture is concerned. Setting aside the effects of valve timing, resonance effects in the intake passage, etc., for the moment, the rate of suction from the engine is proportional to its RPM. The atmosphere is supplying air at 29.92 inches of Mercury through the filter and throttle body to the intake passage . The manifold pressure is 29.92 minus the air filter restriction, minus the throttle body restriction. So for a given RPM, the intake manifold pressure is determined by those restrictions alone, not the load on the engine, as it is affected by the grade or whichever gear one is in.
-
In Ratch's earlier post, he indicated his bike came with cannisters, but his test was done without them.
-
Wow! A lot of water under the bridge since the last time I checked in. First, Dan M's reading of 15" Hg at idle, is about - 0.5 Bar, while the fuel pressure regulator target is 3 bar. So if its reference port is connected to the intake manifold, it becomes 2.5 bar. Fuel flow would be reduced by 8.7%. Improvement in economy would not only occur at idle or closed throttle decels. Part throttle cruising economy would also be improved, although to a lesser degree, if the vacuum is less than at idle. By the way, that isn't necessarily so. Had Dan M's idle vacuum reading been in the 20-21" Hg range, I would expect it to be far lower during cruise, but at 15", I'm not sure at all. I've seen engine vacuums ranging anywhere from 10 to 16" under cruise conditions. Under deceleration, fuel flow would decreased by a higher percentage, due to the higher vacuums achieved. With smart enough software in an ECU, anything which can be done by connecting the FPR to the intake manifold could be duplicated, since it has data on TPS and RPM, BUT only if the air filter pressure loss and barometric pressure is consistent with the software's assumption (there's that dangerous word again!), OR if an ECU's absolute pressure sensor is working and connected to the airbox between the filter and the throttle body, then there's no problem. So under those conditions, mapping the ECU can do the same thing. So why bother considering connecting the FPR to the intake manifold? Because it's cheap! Ratch's comment that his water manometer (Mercury's density is 13.6 times higher) does not fluctuate much lends some comfort that the FPR diaphragm might not be unduly fatigued. Moreover, the worst case for engine pulses would be at idle, wherein the frequency would be lowest. The 0.030" orifices act as a low pass filter, so the higher the RPM, the less the fluctuation. Also, the farther open throttles are, the less the fluctuation. Idle is the worst case for both reasons. If this regulator is constructed in the conventional fashion, its diaphragm is controlling a needle, with fuel pressure on one side of the diaphragm and ambient pressure and a spring on the other. So it's not as though the diaphragm makes a sudden movement when the ambient pressure (vacuum) reaches a threshhold. Still, it is a concern that I don't wish to discount altogether. Would I do it anyway in the name of science and fuel conservation? You bet! I like the cleaner exhaust as well. Based on Dan M's analysis, it's as if the idle mapping was done with it in mind.
-
Holy smoke! I'd better check mine. I recently eliminated the airbox cover and installed Staintunes without baffles. Thanks for the heads up.
-
Ratch, we really need numbers and analysis to determine whether .030" is able to flow enough to affect the regulator, as it appears is intended by the diagrams which show it connected thereto. In terms of circumstantial evidence, when synchronizing with mercury manometers, the columns seem to respond quickly in spite of their mass. I suspect the mass of the regulator diaphragm is a good deal lower. But then, the cannisters are out of the circuit, so the vacuum signal is sensed directly by the manometers, without leakage through the cannister. I checked whether the diagrams showing the regulator connected to the vacuum port have a cannister connected as well. If that's the case, and the cannisters impose a restriction far less than .030, then to that extent the signal to the regulator would be attenuated. At least the diagram in one of the posts shows no cannister connection, just the regulator connected to both TB's. Another question is whether those bikes with the regulator connected also had the .030" restrictors. If bikes with the regulator connected were intended to have no cannister connection which would bleed off the vacuum, and/or have no restriction, but yours has both, that would explain why you saw no difference. Do you have any knowledge of any of these open items?
-
Great! It's a bit of a job on my bike to get the pump/regulator assembly out of the tank and create a leak free port on its mounting flange. If your report shows that it saves any significant gas consumption, now that my bike is out of warrantee, I'll do it and report back as well. If practical, try to use the same brand and grade of fuel and oil throughout, as well as a consistent starting/warmup procedure and tank filling level as well. Avoid doing any tuneup maintenance during the test to keep everything consistent. Sorry if I sound like a schoolteacher! This will be useful information, and if it is conclusive, I'll add the results it to the FAQ section.
-
If it is, there's a thread in the FAQ section on the subject and the tipover valve orientation required to prevent it. There is only one right way to connect and orient it, and it's not the way my bike came.
-
Thanks, Greg. It's kind of you to chime in. Does that mean that anything less than 1100 would have 10 mm screws?
-
Thanks for the quick reply. Now that I think of it, does the Jackal use the same banjo fitting to feed oil to the heads? I learned that the Centauro uses a 10 mm instead of 8 mm. What about the Jackal?
-
Does the Jackal use the same "pork chop" side bracket the footpegs are mounted to? Thanks.
-
As wear progresses, does anyone know whether the clearance opens or closes on these engines?
-
Wouldn't it be nice if the balance could be done at 3K RPM with the engine loaded as if the bike were cruising. The equivalent might be balancing unloaded at some higher RPM, but as Skeeve indicates, his mercury bounces around too much for that. On the other hand, it takes such a tiny bit more throttle to go 3,000 versus just off idle with no load, I suspect it makes little difference whether it's done at 1,800 or off idle or 3,000. For the true perfectionist, here's a procedure to consider. Attach a voltmeter to the TPS. Measure the voltage with butterfly closed and make note of it. Monitor the TPS while cruising on the road at the target speed. Run the bike on a dyno with the throttle held at the measured TPS voltage with the load set to control RPM corresponding to the target speed. Balance the throttles. To make things even more interesting, monitor the F/A ratio and adjust the TPS to achieve the desired ratio at the same RPM and load as above. As power output varies, the physical throttle position may have to be varied to maintain the RPM and load constant, making this an iterative procedure. Shut the bike down. Measure the TPS voltage with the butterfly closed and compare to the initial reading. This will tell you how much offset was required to obtain the desired F/A ratio. If not too far from 150 mv, you could consider leaving it where it is. If it is far from 150 mv, consider having the ECU remapped. If I had access to a dyno, I'd do it just to learn something and see what difference it would make, if any.
-
I agree that snapping the plates closed is risky. Gentle pressure is enough. It's slide rule, not ruler. The latter is used for scribing lines. I agree completely with your last comment. No point in arguing with success, only with ignorance and errors!
-
The intake manifold port used for reference pressure is on the flange screwed to the engine in your picture. It's the same one used for synchronizing the throttles. There is a hose connected to it. Whether you connect the regulator reference to it is up to your judgment. The pressure is set to 3 bar, so the intake manifold vacuum, which can approach 3/4 bar or more, can have a significant effect on reducing fuel consumption, especially when decelerating and at part throttle operation. For an idea on MPG, my bike ran at 38 mpg as delivered. Calibrating the TPS and synchronizing the throttle bodies improved it to 42, a considerable improvement, and it is still breaking in, at only 4500 miles. This will give you a ballpark idea of how efficient your bike is, and whether to consider going through valve adjustment, TPS cal and Synch before doing anything else.
-
Bikes with the fuel pressure regulator mounted external to the tank have a reference port. This is not connected on some bikes, raising the question, of what it is for. This port allows the regulator to vary its output pressure with the intake manifold vacuum when connected to the throttle body intake manifold ports. At wide open throttle, when intake manifold pressure is nearly atmospheric, it has no appreciable effect. At part throttle, it lowers fuel pressure to lean the mixture. My '04 Cafe Sport and other models provide no access to the regulator, as it is internal to the tank. Bikes with external regulators that have the port disconnected raise the question of whether to connect it, and whether the mapping takes the disconnected port into account. Caution: a concern has been expressed that connecting it may lead to early fatigue failure of the regulator because of the pulsating nature of the vacuum signal. For a thorough discussion and connection diagrams, see the following thread: http://www.v11lemans.com/forums/index.php?...0Port&st=30
-
Try this: http://www.v11lemans.com/forums/index.php?...0Port&st=30
-
It is the pressure reference that allows the fuel pressure to vary with intake manifold vacuum. There are diagrams showing it connected to the throttle body port shown in your picture. It has no effect on wide open throttle, when the intake manifold pressure is essentially atmospheric. At lower throttle settings, it will slightly lean out the mixture. My Cafe Sport has the fuel pump built into the tank, so it is not connected and inaccessible. I assume (hopelessly optimistically) that the factory tuning takes this into account on my bike. That leaves the question whether your mapping takes the disconnected port into account, or whether it is supposed to be connected. There is a thorough discussion elsewhere in this forum with diagrams. I'll see if I can locate it. If I had the port available, I would love to run a tankful with and without it connected to see if it affected fuel mileage. Good luck with the bike. It's a beauty.
-
Hi docc, I used a high copper content anti sieze. Copper is a better conductor than zinc. My plastic holder shattered upon removal. I had the brass fitting handy. As an obsessive type, I researched the copper content on various brands. The Permatex 765-2569 sold by NAPA had a high percentage of copper. I believe the brass replacement is a worthwhile improvement. I covered the fins with the high temperature aluminum foil tape used for furnace ducting to reduce the heat transfer to ambient air because I wanted the sensor to be as close to the engine's internal temperature as possible. best, John
-
Of course it is true to say you would be offsetting the balance previously created. I think Micha's intent is to keep the procedure simple. His method balances at 1800 RPM as a priority over balancing at idle. I agree with that priority, and would do without the final balancing at idle. Those who want to take more care can use the iterative balancing procedure in the How To section. Let's try another example using Micha's method. Suppose the TPS is calibrated correctly, 150mv at throttle closed. Air bypasses are opened 1 full turn and left there. At 1100 RPM, it so happens that the TPS indicates 3.9 degrees. Micha says adjust the TPS to read 3.6 degrees anyway. The result is a leaner mixture throughout the throttle range. Measurements of TPS voltage at WOT are subject to the accuracy of the 5 volt reference voltage. What if the reference voltage is off by 1%, which is not unreasonable to expect for the typical reference chip? Then the 5 volts can be anywhere from 4.95 to 5.05, a range of 100 mv. Measuring the difference between the 5 volt reference and WOT is better. However, a 1 degree unbalance at WOT has little effect, whereas a 1 degree unbalance at off idle and cruise has a big effect. What if the ratio of linear cable motion to butterfly rotation varies between throttle bodies? For any and all of these reasons, I strongly suggest using the lower end of TPS range for calibration.
-
Micha's method compared to the How To method: Step one - Set your valves to world settings Step two - Set your bleed screws to open 1 full turn Step three - Synch throttle bodies at just off idle (around 1800 rpm) Step four - Set idle to 1100 using left idle screw adjuster only Step five - Set TPS to 3.6 degrees (I forget what that translates to in mv..someone here will know) Step six - Ensure idle trim is set to zero One important difference is that the How To method leaves nothing to chance, whereas the Micha's method takes shortcuts by making assumptions. For example, it assumes the left idle screw controls both throttles and that the right idle screw and fast idle is not in contact. Synchronizing the throttle bodies at just off idle should eliminate interference from the two idle screws so that the connecting rod is in control, just as in the How To method, except that any variation in the flow rate delivered by the two bleed screws will require an offset of the two butterflies in order to compensate. The assumption here is that the difference is negligible. The How To method avoids this interaction. The How To method quotes 521 mv as the middle of the published ranges as a guideline. That corresponds to 3.5 degrees, almost identical to Micha's 3.6. The other important difference is that Micha's method apparently disregards the 150 mv at throttle closed baseline calibration in favor of forcing the TPS to be adjusted to 3.6 degrees (532mv) at 1 full turn of bypass opening and 1100 RPM. In the case of the How To method, the TPS is calibrated at throttle closed, and if air bypasses are not opened at least 1/2 turn to achieve 1100 to 1200 RPM, then the idle screw is loosened by closing the throttles in steps (which will reduce TPS voltage) until they are. Let's try an example using Micha's method. Suppose the TPS is calibrated correctly, 150mv at throttle closed. Air bypasses are opened 1 full turn and left there. At 1100 RPM, it so happens that the TPS indicates 3.0 degrees. Micha says adjust the TPS to read 3.6 degrees anyway. The result is a richer mixture throughout the throttle range. In my opinion, so long as the assumptions the Micha procedure makes are reliable, it has merit provided one is willing to accept the fact that it will likely result in an uncalibrated relationship between TPS voltage and actual throttle opening. For some riders and bikes this may be entirely satisfactory. However, it is important to understand that maps provided by others which one may wish to use as is, rely upon a TPS calibrated to the throttle closed baseline. The How To method should be used when setting up the bike for dyno tuning or using a map provided for a particular set of modifications or special purposes as is. A lot of this has been gone over in previous posts. I just thought I would summarize it from my point of view. regards, John
-
It seems to me that as long as the oil level is below the plate, it provides protection from windage and whatever contribution that might make to oil consumption. If I have a choice between one which allows 4.5 quarts, and one which allows considerably less because it is mounted lower, I prefer the former. I agree with Pete that Dave might investigate the cause of his relationship between oil level and consumption. If it's windage, it seems to me that Pete's plate would work as it is. If it's something else, Pete's plate won't hurt, but would cure the starvation problem under fast acceleration, and allow for more oil.
-
My bike runs about 60 mph at 3,000 RPM, from recollection. If so, at 73 it's doing 3650. My philosophy is somewhat different from yours and Murray's (except I think he missed my earlier post suggesting changing the 6th gearset ratio). I don't feel the need to keep the RPM's in a range that allows turning up the wick for instant torque reserve when I'm spending lots of time on the slab at a constant 73. I believe in the best maintenance and tuning as my form of TLC, but happy to run the engine at lower RPM with taller gears, as long as they are high enough to maintain decent oil pressure. I come from a background when Honda's big engine was the 450, and I did everything practical to change the primary and final drive ratios on my Harley to drop the RPM's. With wife in the sidecar and vacation and overnight camping gear on board, I would lug that 1200 cc beast up long hills in top gear with wide open throttle whenever necessary, and only downshifted when it wouldn't hold 55. I had designed a diagnostic panel for it which had an LED energized by the points on each cylinder. You could practically count the pulses. On another 10,500 mile trip across the country, down to Mexico and back in July, I did the same thing with my Honda 450, fully loaded with wife, full camping gear, etc. Neither engine showed any signs of harm. When I learned that Mercruiser's V8 engines were purchased from the same assembly line GM used for cars, I gained a great deal of confidence in the basic ability of piston engines to be able to run long term at much higher loads than they encounter on cars and bikes. Mercruiser simply made the changes to "marinize" the automobile engines. I might be missing something about the idiosyncracies of Guzzi engines, but I suspect that they are just as robust, based on comments from people like Pete Roper and others.
-
I like that squirrel chaser option!
-
I like having a real tall top gear just for long distance slab cruising. I typically do 73 when the limit is 65, and higher when the limit is higher, or when I'm buzzing along with lots of others doing the same thing. E.g. on the New Jersey Parkway, the posted speed limit is 55. The average speed in the two fast lanes is 75, even when traffic is heavy. Under those conditions, going with the flow is the safe way to drive and saves time, too. Seems to me the 1100 is up to the task of a taller top gear for cruising purposes. Unfortunately, in taking a look at the service manual, near as I can tell, the driven 6th gear is already about as small as it can be. Thought I had a neat project to work on, now that my warantee is about over. I'm sure something else will come along.