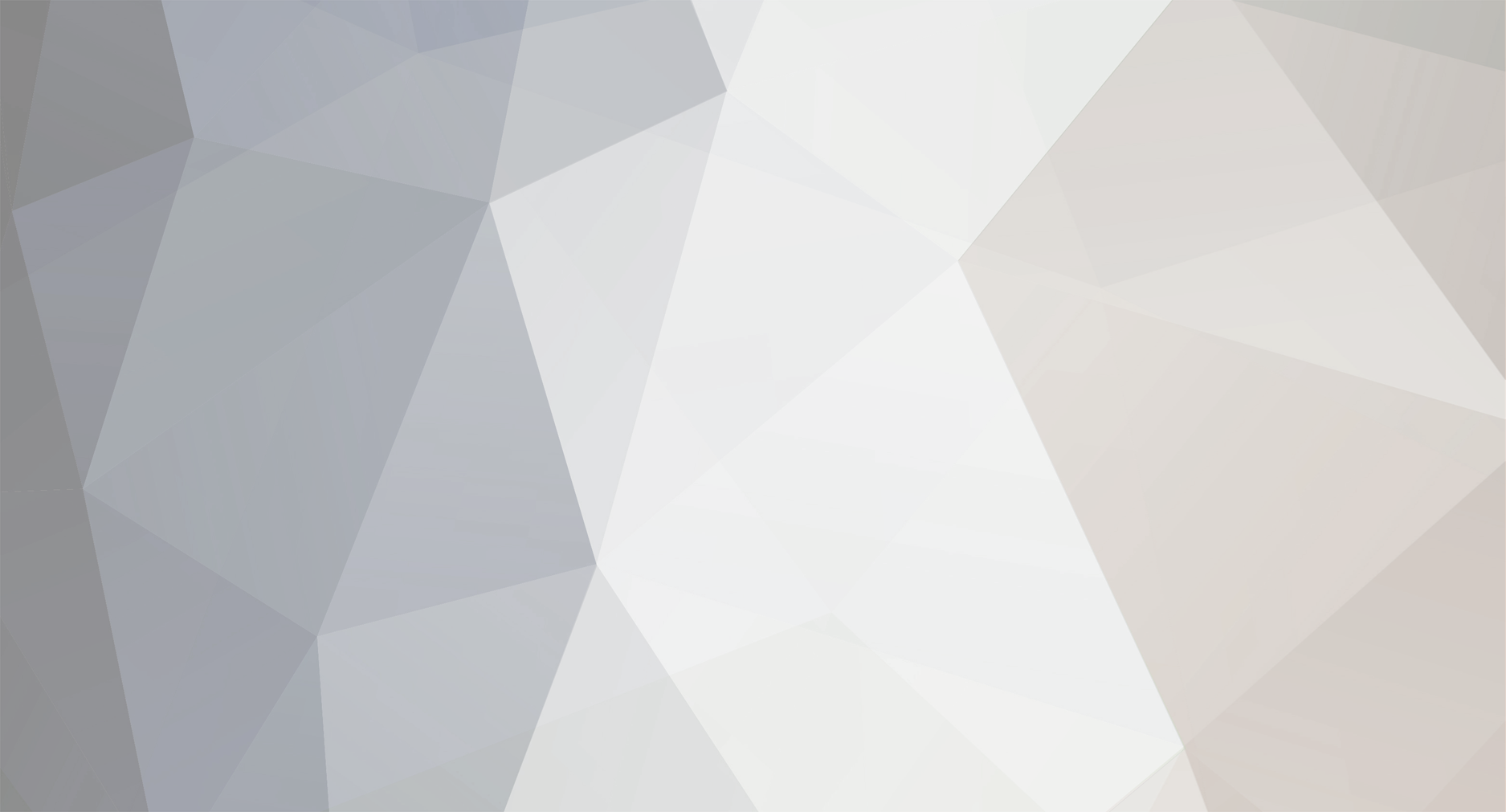
Meinolf
Members-
Posts
169 -
Joined
-
Last visited
-
Days Won
17
Content Type
Profiles
Forums
Events
Gallery
Community Map
Everything posted by Meinolf
-
Hi, it's version 93_6, dated 2017.08.31. Cheers Meinolf
-
Hi, I still get frequent requests for the latest V11 BIN. During the last 2 years my activities have moved on to other bikes, Guzzi Jackal, Norge 1200 2V, Aprilia Mana GT and Aprilia RST 1000 Futurua. So I didn't have the time and inclination to do further work on the V11 BIN. This will likely change, as I plan do some work on my V11 (suspension, cylinder head porting, valve & valve guides, valve timing, ...) during this winter. Also the experience gained since scrapping the unreliable and error prone Innovate LM2s and moving on to the Zeitronix ZT-2s plus a enhanced set of software tools (programmed by Beard) have led to better data logging and analysis quality. If I get usable results for the V11, I'll share them with you. In the meantime the V11 BIN can be downloaded here: https://drive.google.com/open?id=1e7MMuO6vrUZGFfmkCtL3zsW1qeS6uDgY My recommendation for the basic setup, which is tightly linked to the BIN, is: - CO trim set to 0 (using GuzziDiag or directly changing the EEPROM value) - Both bypass screws completely closed (I could have built the BIN and fuel values with opened screws, but this would have introduced an additional error source. My half turn open is likely different from your half turn open. Completely closed is rather unequivocal in comparison). - TPS baseline set to 157mV (The 150mV found in the service manual and many other places in the internet are wrong, the Marelli or Guzzi engineers had rounding errors in their calc. 7mV are not much, but why not do it correctly if setting it anyways) - Idle sync using the two throttle stop screws (I've explained the reason several times already. The play in the diverse parts of the throttle opening and the spring push (throttle closed) versus cable pull (throttle open) operation makes this the only way to get a sync at idle as perfect as possible. While my V11 is mostly stock, I introduced several changes. One is the bell shaped opening of the intake snorkels, another one is the rework of the throttle butterfly valves and their shafts. These, and the TI cans I'm using, have increased airflow thru the engine. Meaning that bikes which do not have a similar airflow or, for example, have the airbox removed (very bad decision), will run richer than required. If you believe this is the case, just reduce the left cylinder fuel values in small steps until you are satisfied. DO NOT change the right cylinder fuel values or you will loose the biggest advantage of the BIN, which is synchronized Lambda/AFR values across the cylinders. Cheers Meinolf
-
Hi, Beard's PayPal name is guzzidiag@gmail.com. The Guzzidiag software has a clickable link to PayPal using this email address. Cheers Meinolf
-
Hi Tom, the pleasure was mine. Cheers Meinolf
-
Hi Dave, I don't know if the hardware of the ECUs used is exactly the same, the additional identifier (16Mxxx) on the ECU label would help in answering this. The code used in the Duc BINs is similar or identical (given the hardware of the bike is the same) regardless of the bike's make. Marelli uses a code library approach, many code sections can be found in all ECUs (P8, 16M, 15M, 5AM and even 7SM, though this one uses an inline coding technique). Cheers Meinolf
-
Hi, why would one continue to use a PC after direct editing of fuel maps became possible escapes me. The PC is a wart on top of the ECU and the axis values don't match the ones used in the BIN at all, with all the detrimental effects resulting thereof. Which could be rectified, the Dynojet Power Core software allows changing the TPS % values and adding additional columns. They could be brought much closer to the degree values, at least on the 15M, where the low degree values can be represented with % values to a sufficiently good enough approximation. And Dynojet, upon request, also changes the rpm values and columns. Cheers Meinolf
-
Hi, first and foremost the the peaks and troughs are a reflection of the volumetric efficiency of the engine. Air mass going into the combustion chamber does not increase linearly with rpm or TPS opening. Cheers Meinolf
-
Hi, yes, the MCU is a 68HC11. All ECUs (Marelli 15M/59M/5AM and Sagem 1000) whose code I've dissassembled use raw look-up tables for the digitalized input and a conversion look-up table. The raw values are only used for out-of-bounds checks, most of the code uses the converted values. Which makes sense, as most raw values are reversed - low raw values equivalent to high converted values - and using a look-up table saves some code and computing time to reverse the data. And look-up tables make it easier to adapt to new sensors, be it NTC, potentiometer or whatever. Cheers Meinolf
-
Hi, and just to close this off. The 157mV I recommend as TPS base setting stems from the TPS ADC look-up table in the BIN. Guzzi, or more likely Marelli, made a stupid mistake in this table because a wrong rounding was used. The ADC in the 15M/RC is a 8bit device, translating the (analog) voltage coming from the TPS into 256 digital steps. 5V divided by 256 equals 0,01953V. The difference between 150mV (factory recommended value) and 157mV is quite small, in fact if falls under the graininess of the ADC function (look this up in the web if interested), but why use a wrong value if the correct one is known. Cheap blueprinting, as it is. Cheers Meinolf
-
Hi, the butterfly valves should be firmly seated against the throttle body. In fact the butterfly valve contact areas are slightly tapered (no sharp right angle edge) to ensure a consistent seating without hammering into the throttle body. I've found that getting consistent (+/- 1 or 2mV) readings if using the same force to completely close the valves is standard. The variations you mention might well be due to worn out throttle shaft bearing(s). I've used standard bushings to replace the original ones if the play became to large. Cheers Meinolf
-
Hi, the recent discussion about optimized BINs has revived the interest in the BINs I created for the V11 (and Jackal) with a 15M ECU. Those having 2V CARC models might be interested in this one: https://wildguzzi.com/forum/index.php?topic=100576.0 Cheers Meinolf
-
Hi, re a) My comments above refer to the idle sync. The running sync should be done as described in the service manual. This will take up the lash in the connections between the two throttle valves. Removing this lash has no impact on the breakpoint sync done with the idle sync procedure. As written in my previous post, this becomes much more obvious if the system is closely looked at and considering in which direction the lash works. re b) If using one of the throttle stop screws will achieve both the synchronicity and the desired idle rpm, that's all right. I've found that getting both right typically requires both screws. Cheers Meinolf
-
Hi, your reasoning is quite correct. However, there's a lot of combined play in different bearings. And only with zero play would setting the connecting rod clash with the throttle stop screw setting. Taking a close look at the mechanics will make this more obvious. Cheers Meinolf
-
Hi, consider the following. The BIN contains two fuel (and ignition) maps, these are indexed by rpm and TPS and each rpm/TPS breakpoint contains fuel values. The main maps contain values for the left cylinder, the delta maps for the right cylinder contain the differences to the main maps. So a breakpoint in the main map might contain the value 100, the corresponding value in the delta map could be 10 (or -10). Which is added (or subtracted) from the main map value, so the value pair would be 100 and 110. These fuel values would achieve a given Lambda/AFR at a given airmass going thru the engine at this specific breakpoint. The airmass going thru the engine is determined by several engine specific characteristics and the opening of the throttle butterfly valve. The free area through which air can flow is described in a rather complicated cosine function, which also takes into account the diameter of the shaft and the thickness of the butterfly valve. The nature of sine/cosine functions is that they are not linear. Accordingly a very small rotation angle change from closed state would result in the same free area than a much larger angle change, say at halfway open. The TPS breakpoints are staggered very closely at the beginning, the steps would (for example) be 2.0°, 2.6°, 3.2°,.... At higher settings the breakpoints much farther apart, say 45°, 55°, 67°, 81°. But, with well choosen breakpoints all steps would result in linear increase of airflow, or rather airmass, moving into the combustion chamber. The essence is that at low TPS openings appearently minor changes have the same effect than much larger ones at bigger openings. The BIN and the included maps are not very carefully designed in the first place. They are acceptable for, say, 95% of all engines, deliver poor results with 4% of the engines are are perfect for 1% of the engines. Which, if one considers the priorities of a manufacturer, deviations from the blueprint due to mass production differences in all components, wear of said components and other changing parameters, such as gasoline mixture during the last 20 years, is not too bad. So the question is how to accurately align TPS breakpoints. Opening angle is not practical to measure, so indirect airmass flow is chosen. Indirect because synchronization uses pressure as an analog to airmass, which together with the fuel generates a certain force with which the cylinder is moved downwards and results in a partial vaccum. Springs are used to force the butterfly valves closed. The throttle stop screws act against the spring pressure and take up any loose play. Thus using the throttle stop screws for sync'ing gives a start non-variable position. My BINs contain fuel values in the main and delta maps tailored for a specific Lambda at any breakpoint. If the idle sync is not done as described the result will be that these fuel values at specific breakpoints no longer match. So, to use above figures, instead of having a value pair of 100 and 110 the value pair might be 100 and 120, because the next delta map breakpoint value is being used. The result would be different Lambda value for each cylinders. Which means the cylinders are working against each other. Allowing a user to loading a different BIN with edited maps was not intended by Marelli. Instead CO trim and bypass screws were the intended methods to correct differences between the two cylinders. CO trim influences fuel delivery, bypass screws influence air delivery. The effect of both methods tapers of with increasing fuel values (CO trim) and increasing airflow (bypass screws). So I've chosen to use fuel values which, with CO trim set to 0 and bypass screws closed, are on target. I could have chosen fuel values which provide the same Lambda with a CO trim of 100 and bypass screws 5 turns open, but why would I introduce 2 variables? Cheers Meinolf
-
- By idle screw you mean one of the throttle stop scews? Don't use this procedure with my (or any) BIN. The main and delta fuel values are synchronized at every breakpoint. If you change the idle throttle of one throttle only then you lost the synchronization between the TPS breakpoints. Sync'ing in idle is the only way to match the TPS breakpoints. And it's especially important in the low load area because the TPS breakpoints are spaced so tightly. Getting this and the base line setting of 157mV right are the single most important steps. The V11 TPS placement on the right side is rather unfortunate because wear-prone connections introduce play. Cheers Meinolf
-
Hi Richard, changing the program code is VERY difficult, because even using one different opcode might impact the very tight timing sequence of the code. We (Beard, myself) made code patching tests, but abandoned them for this reason. And, the code of the latest OEM BINs works well and reliably. I can't remember offhand all of the parameter changes I made, but this will give you an idea - RPM and TPS legends - Warmup table legend - Baro legend - Warmup table content - TPS look-up table - Engine temp trim correction - Air temp/air pressure correction table content - Idle ign - Main ign - Idle fuel table - Main and delta fuel table - plus other stuff I've already forgotten Cheers Meinolf
-
a BIN is always the complete software, both program code and parameters. Cheers Meinolf
-
Both the bypass screws and the CO setting date back to times when the BIN couldn't be changed and where the only possible means to correct variations inevitable in mass production and the unavoidable wear. Since Beard created the means to down/upload the BIN this has become unneccessary. I choose to use a CO trim of 0 as base for my fuel map optimization as the CO trim effect tapers off with increasing rpm, or rather increasing air flow. The closed bypass screw setting was used because it's easier to duplicate a setting of totally closed than 1 turn open. Somebody elses 1 turn is likely to be different from mine, even small variations matter in idle. The fuel map values at those breakpoints where CO trim or bypass screws have an impact are so that the mixture is correct with my recommendations. As my V11 was somewhat modified with conical opening of the snorkels, removing half of the shaft holding the butterfly valve, re-worked butterfly valve contours, TI cans, valve play set to 0.3mm for intake/exhaust to countermand the very long ramp up slope of the camshaft and the resulting loss of mean pressure, an average V11 would run a bit richer than mine. Still I would recommend to reduce the (left cylinder only) fuel values across the entire fuel map in small %-steps instead if trying fiddle with CO trim or bypass screws. Cheers Meinolf
-
A PC doesn't alter any sensor readings going to the ECU. It modifies the injection pulse width based on the map values. In itself not a bad approach if the ECU's content (BIN) can't be modified. I use a PC on a Yamaha GTS1000 to shift the Lambda value, as seen by the ECU, downward by 0.03. The challenge with a PC map is that the breakpoints, neither TPS nor rpm, match the breakpoints used by the Guzzi (or whatever) code. Thus the bi-linear interpolation of the ECU code between the given breakpoints is taken over by the %-variations of a PC map at breakpoints which don't match. The TPS breakpoint issue could be avoided with the Dynojet Power Core-SW to set individual breakpoints, but I've never seen a PC map which actually used this. Changing the BIN loaded into the ECU is always the better choice. Cheers Meinolf
-
Hi, that's what he said and that's what he still does. Send a PM with your email address. Cheers Meinolf
-
Hi, setting the TPS baseline is the first step. Remember, all connections to the throttle must be removed before adjusting the voltage. The valve play should be at least 0.2mm for Intake/Exhaust. 0,3mm is my recommendation, the V11 camshaft has very! long ramp-up slope, >100°. The standard setting will result in sligthly opened valves in that area, resulting in mean pressure loss and decreased valve cooling. Once this is done sync the throttles in idle, try to keep the bypass screws completetely closed and do the sync with the throttle stop screws. CO trim should be set to 0 initially and only be changed if you have no means of actually measuring AFR. GuzziDiag always works, but a KKL adapter with an original FTDI chip is needed. There a lot of counterfeit chips in the market, they will mostly not work. Cheers Meinolf
-
Hi, here's a complete breakout cable: http://www.casperselectronics.com/cart/index.php?route=product/product&product_id=853 Cheers Meinolf
-
Hi Rich, the TPS is a potentiometer. The voltage is measured between signal ground and the wiper. You probably know that the throttle must be completetly closed when setting the baseline to 157mV - using a DMM, software measurement via GuzziDiag will not work. Rotating the TPS changes the relative position of the wiper, hence the voltage changes. Cheers Meinolf
-
Hi, that's an easy one. https://www.von-der-salierburg.de/download/GuzziDiag/ http://www.tunerpro.net/downloadApp.htm Cheers Meinolf