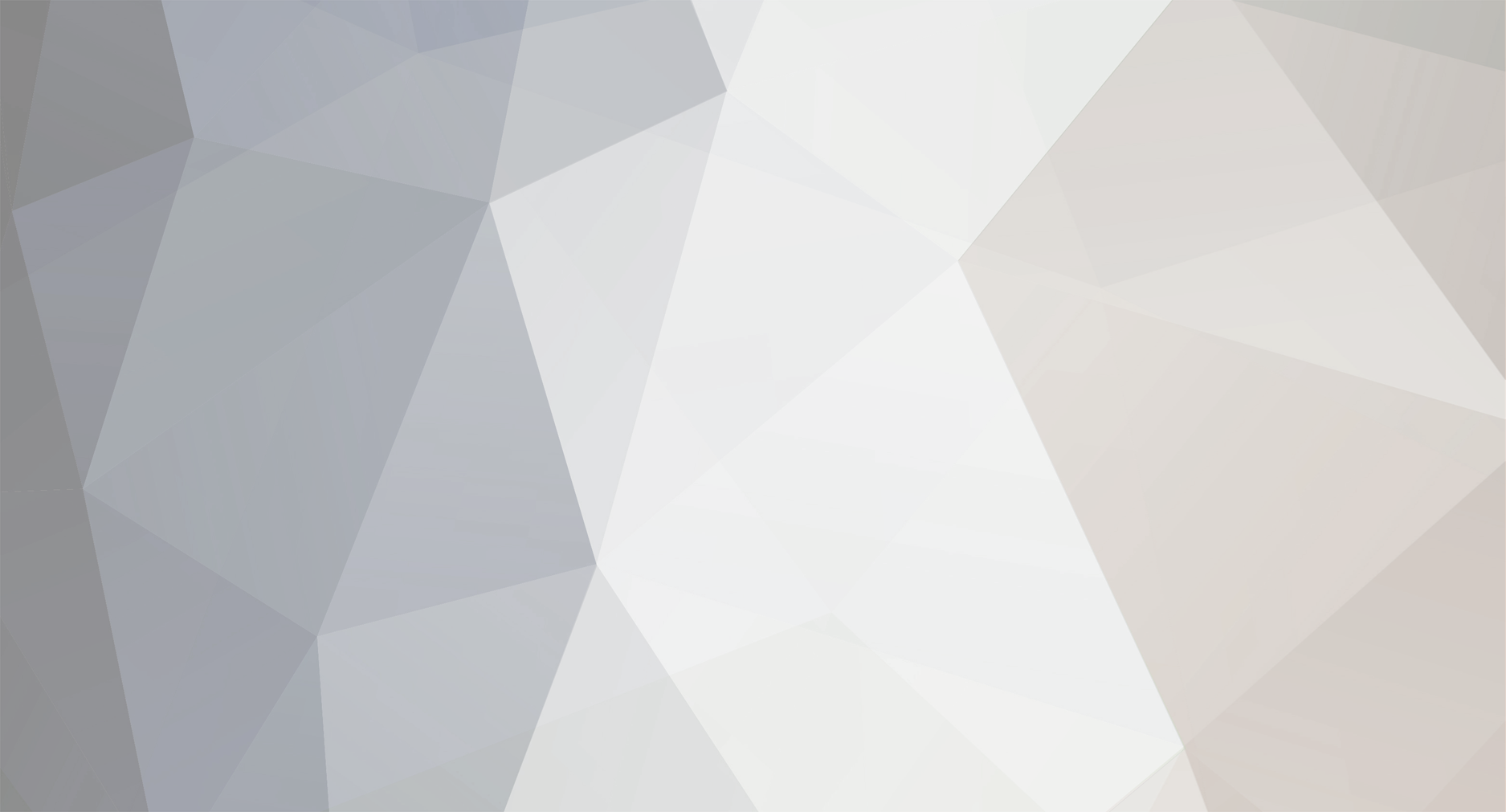
Meinolf
Members-
Posts
169 -
Joined
-
Last visited
-
Days Won
17
Content Type
Profiles
Forums
Events
Gallery
Community Map
Everything posted by Meinolf
-
Hi, Meinolf also explained that the CO trim, as it adds or subtracts a constant value, is NOT a global enricher A value of 1 in the fuel map equals 64μs injector opening (or more properly voltage applied to the injector). So a CO trim of 1 corresponds to ~7% of a fuel map value. Low load values in the fuel map can be ~25, highest values are >200. An increase of CO trim by 10 equals ~3% (10 x 4.76μs) / (25 x 64μs). At WOT the increase would be ~0.037% (10 x 4.76μs) / (200 x 64μs). So the influence of the CO trim is most noticeable at low fuel map values and lessens quickly as the fuel map values increase. But, if one bothers to measure AFR and adjust the fuel maps accordingly, why do so with an unneccessary influencer like CO trim? Keep it at 0. Cheers Meinolf
-
Hi Marty, John, Editing, reading and writing the EEPROM content is not different from doing the same with a BIN. - Connect the computer to the ECU - Turn on ignition, but don't start the engine - Start EEPROM Reader/Writer - Press either Read or Write - Done, turn off ignition Editing the .EEP file is just as easy. - Tunerpro doesn't recognize .EEP, so rename to .BIN. - Load the renamed file and the EEPROM XDF into Tunerpro - Change the CO value. - Save the file and rename it to .EEP - Write it to the EEPROM using the procedure above. The 15M program code uses very few parts of the EEPROM data, so there's nothing harmful which can happen. Cheers Meinolf
-
Hi John, Yes, I meant that the description text was changed. Cheers Meinolf
-
Hi John, changing the EEPROM to adjust the CO trim is easier and faster than adjusting with GuzziDiag. The EEPROM Reader/Writer and the XDF is available on Beards website. If you see values in GuzziDiag then it has connected to the ECU. The absence of any info just means that the content was edited. Cheers Meinolf
-
Hi, a short update. I haven't yet received the PF1C I ordered from AliBaba, but Beard already programmed a patch to the 537-BIN which I tested on my ECU test bed over the weekend. He's added code to the BIN which uses an offset to the ADC-values, which are stored in an unused address of the EEPROM. And it, after ironing out a small bug, works. So the proof of concept is done. The basic idea is to use the offset value stored in the EEPROM value, ranging from -127 to +128, to base-line the actual voltage delivered by the PF1C at a given setting to the TPS look-up table. We are still mulling over the setup procedure, though. After receiving the PF1C I'll attach it to a throttle body and see which setup procedure works and is easy to use. The current idea is to measure VActual - VTarget at completely closed throttle and divide the difference by the steps of the 8bit ADC, 0.0196V. The result would be the offset used in the EEPROM value to align the TPS and the look-up table. Cheers Meinolf
-
Hi, a short update. Concerning the PF4C, Finland comes to the rescue. MotoMatti (https://translate.google.de/translate?hl=en&sl=fi&u=http://www.motomatti.fi/&prev=search) built a contraption to measure angle and voltage. A friend will send him a PF4C, so eventually we will have the curve of the PF4C equation. Jeff, the CEO of CA Cycleworks, replied to my inquiry. Unfortunately he hasn*t measured a PF4C. And, more great news. Beard (the wizard who programmed GuzziDiag) found out which which addresses of the EEPROM need to be changed to adopt a PF1C (that's the TPS with a known linear curve but holes instead of oval openings). I ordered a PF1C on Alibaba (11$ incl. shipping) and will test it on my ECU bench upon arrival. And the TPS lookup table can be taken from most 15RC BINs, as the PF1C is the OEM TPS. So, all is well Cheers Meinolf
-
Hi Martin, Hubert knows what he's talking about. I'll send an inquiry to CTS. Roy and I had an exchange about the the Hall effect sensor some time ago, but I didn't follow it up. Roy, did you? Cheers Meinolf
-
Hi Martin, do you know that CTS is the supplier of Magneti Marelli? I won't fish in the dark. I contacted Chris, the owner of CA Cycleworks, and asked if he had data for the PF4C. He made an amazing contraption to check and record the values of TPSs. Really cool stuff! https://www.youtube.com/watch?v=cZK9fVvNaC4 Beard (author of the GuzziDiag suite) made an interesting proposal. Which is to use the PF1C. Because it doesn't have the oval holes necessary for rotation, he would modify the contents of the EEPROM and add an offset. And we could adapt the TPS lookup table to the linear curve of it. The PF1C is available for ~11$ from Alibaba, so I went ahead and ordered one. Cheers Meinolf
-
Hi, finding the curves is less trival than one might think. I talked with Marelli in Germany, but they have no clue whom to ask in their operation or even which division to ask. The same with two distributors in Germany. And sent an email to Jeff. Alas, the address is not valid. An easier way might be to contact HD's support and ask the question. The HD part # is 27271-95. Does anybody have contacts to Harley and ask? Cheers Meinolf
-
Hi, @Docc. Yes, 2 points (angle/voltage or angle/resistance) are sufficient to create the linear equation describing a straigt line. The http://img4.hostingpics.net/pics/484669PF3CPF4C.jpg doesn't show values, so no reverse calculation is possible. @Martin. The drawing in the link is for the PF3C, for which the equations are known, and doesn't include voltage. The poster "Guest_Jeff in Ohio_*" mentioned that he also has a diagram for the PF4C. Does anybody know him? As the PF4C is used on HDs, the info needed might be available in the Harley community. Does anybody have contacts there and could ask the question? Cheers Meinolf
-
Hi, some advise that the (cheaper) PF4C can be used as replacement for the PF3C. To the best of my knowledge the curves are different, so it's not a drop-in replacement. The TPS lookup table in the BIN needs to be adapted. I'm happy to do so and publish it here, but need the characteristic curve equation of the PF4C for the purpose. I couldn't find anything in Google. If any of you has the means to measure angle and resistance (or voltage), then 4 datapoints would be sufficient to calculate the equations. 0°, 20°, 35° and max. ° would be enough. Of course getting the equation(s) would be even better. Cheers Meinolf
-
Hi, whatever the version will be after I'm satisfied. I've just switched to a ZT-2 datalogger and am checking against previous measurements with the LM-2. Cheers Meinolf
-
Hi, here http://www.endtuning.com/afr.html are answers to your questions re max. power / max. efficiency. Using the LC won't really help you in creating fuel tables which are in sync and spot on for a targeted mixture. Logging and analyzing the logged data is a prequisite. You'd need a LM-2 or ZT-2 for that purpose. As to your remarks to different air temperature and barometric pressure. Yes, the trim curves in the MG BINs, at least 15M/RC, are way off and do not correspond to the general gas equation. That's why those where the first trim tables I corrected in the BINs. Closed loop as such is not a bad approach. The problem(s) in real life arises out of the pecularities of the narrow band sensor and the hysteresis effects of any control system. The narrow band sensor is really an On/Off device - to lean or to rich. An better approach is to either disable the sensor in the 15RC (and use a BIN suited to the purpose) or move to the 15M entirely. The only difference is that I have a good understanding of the 15M and based BINs thereupon, the 15RC, which is using program code which differs significantly from that of the 15M, is still being analyzed. Send me a PM, if you want to use the 15M BIN I have developed. Btw, the BIN I sent to many of you during the last years is constantly being updated. Contact me if you are interested in the current version. Cheers Meinolf
-
Hi, no, you can't reprogram a 15M to the 15RC code. You could get the 15RC code into a 15M by physically changing the EEPROM. But this wouldn't work as the HW of the ECU is different and the 15M doesn't have the internal wiring needed for a O2 sensor. What you can do, however, is to use wideband controllers such as the LM-2 or ZT-2, which provide, based on the WBO2 sensor, the narrow band O2 sensor voltage as analog output and feed this into the 15RC sensor connector. But, you would then have the same input into the ECU as with the original narrow band. Nothing gained, except for additional HW and installation/configuration effort. What are you trying to achieve? Cheers Meinolf
-
Hi, this probably needs some more details. The 10μs pulse width are correct if the CO trim multiplier in the BIN, which can range from 0-200%, is set to 200%. At 100% a CO trim value of 1 corresponds to a injector pulse width change of 4.76μs. Cheers Meinolf
-
Hi Darryl, following the complete text of the message I send Marty. Does this clarify things? Cheers Meinolf Re CO trim. The values of CO trim influence the injector opening time, plus values increase and minus values decrease it. But, the changes are not specific to any breakpoint. They are applied across the board. Look at below sample calculation. At the top a base fuel map, then the base fuel map + 10 (CO trim), then the percentage changes of the resulting injection time. The result is a generic change. Now, the entire idea of improving the BIN is to get as many breakpoints to a desired AFR value on both cylinders. CO trim can’t effect this. My BINs are based on CO trim being zero. Using it nevertheless only serves the purpose of adapting a BIN tailor suited to my bike to one with a different setup. I recommend to set the trim to 0 and judge the drivability and economy on the road as you aren’t measuring and logging AFR. The CO trim value is not part of the BIN. The value is stored in the EEPROM in the ECU, and that’s not read or written with the Reader and Writer software. Beard wrote an additional program IAW15xEEPROMTool to read/write the EEPROM. While the CO trim can be set with GuzziDiag, using this tool is easier and faster. The engine doesn’t have to run and reach a minimum temperature. http://www.von-der-salierburg.de/download/GuzziDiag/IAW15xEEPROMTool_V0.04.zip http://www.von-der-salierburg.de/download/GuzziDiag/xdf/15M_EEPROM_V1.01.zip
-
Hi Chuck, same as everone else, I'd say. Send me an email or PM. Cheers Meinolf
-
Hi, you can't. Cheers Meinolf
-
Hi Docc, the CO trim value equals 10μs pulse width of the injector (if the CO trim factor is 1), which is added to the respective fuel map value at a given breakpoint. As the fuel map values typically increase with TPS opening and increasing rpm adding/subtracting a constant leads to different results of the influence the CO trim. The fuel map value equals 64μs pulse width, so an increase of one would prolong the injector pulse width by 0.156% (10/64). Translating this into AFR is a totally different game. The pulse width of an injector does not directly translate into AFR, as the current applied to the injector consists of ramp-up, steady, ramp-down and bouncing. During ramp-up the injector flows less at it's not fully opened. With the means at my disposal I couldn't calculate the influence. CO trim was the only method of changing the injection time prior to the development of Beard's GuzziDiag suite. With the capabilities now available CO trim is obsolete. Cheers Meinolf
-
Hi Darryl, I've corrected the trim tables for air pressure & temp and engine temperature. Based on this all fuel maps, acceleration map, main and idle ignition maps, ignition retardation following temp/pressure, cold start map and the like were changed based on the AFRs data logging produced and the target AFRs I'm using. Comparing BINs is not a straightforward comparison of one map versus another. So many factors influence the actual opening time of an injector, a value in the fuel map is but a starting point. It goes like: ((Fuel Map value x Fuel map value factor) + (CO trim value x CO trim value factor)) x trim factorairtemp x trim factorenginetemp x trim factorairpressure x trimfactorbatteryvoltage x trim factorn = injection time Cheers Meinolf
-
Hi Camn, just cosmetics, but already corrected. Cheers Meinolf
-
Hi Docc, the logging option logs data to a file, the graph option shows a graph. And Guzzidiag must be connected in both cases. Cheers Meinolf
-
Hi Docc, the table in my previous post was taken from Tunerpro, not Guzzidiag. Within Guzzidiag you see the graphs or create a log by selecting value logging in File -> Settings -> Extras. Cheers Meinolf
-
Hi, no difference between the two in regards to programmability. The 15M is better understood, though, and the XDF is much more comprehensive. I am enhancing the 15RC XDF based on my 15M XDF using the source code of both types, but this doesn't have a high priority, my bikes all use the 15M. The only difference in functionality between the M and RC is that the latter supports closed loop operation with a narrow band WBO. Which one is better of disabling anyway, so you could just drop in a 15M. It's a straight replacement Getting rid of the airbox is not good for anything except noise. And tuning the fuel maps in the low to medium load areas is going to be a nightmare. I would't do it. Cheers Meinolf
-
Hi, a) Have you checked and confirmed if the TPS is defective? With GuzziDiag you can perform a fast but very reliable check if something is amiss without touching the TPS itself. Select Diagram in the View section and slowly open and close the throttle. The resulting curve should be smooth and consistent with a knee at 30°, beginning where the TPS has a different resistance curve. b&c) The PF3C used by Ducati is the same one as on Guzzis. Going by the curve shown by Cycleworks this is the one you need. d) You can use any TPS which can be fastened to the throttle body. If it has a different curve then the TPS lookup table in the BIN has to be changed so that the voltage delivered by the TPS at all openings corresponds to the values in that table. Most of what needs to be known to understand the TPS operation was already explained here: http://archive.guzzitech.com/HD-TPS-Jeff_B.html Below picture shows the TPS lookup table from a 15M. The lower table is not part of the BIN, it's just a calculated table to show the voltages corresponding to degrees with a PF3C. Adapting the TPS lookup table to TPS with a different curve is quite simple. Use the curve formula of the TPS and calculate a table with corresponding degrees and voltage breakpoints. Change the values in the TPS lookup table accordingly and it's done. Cheers Meinolf