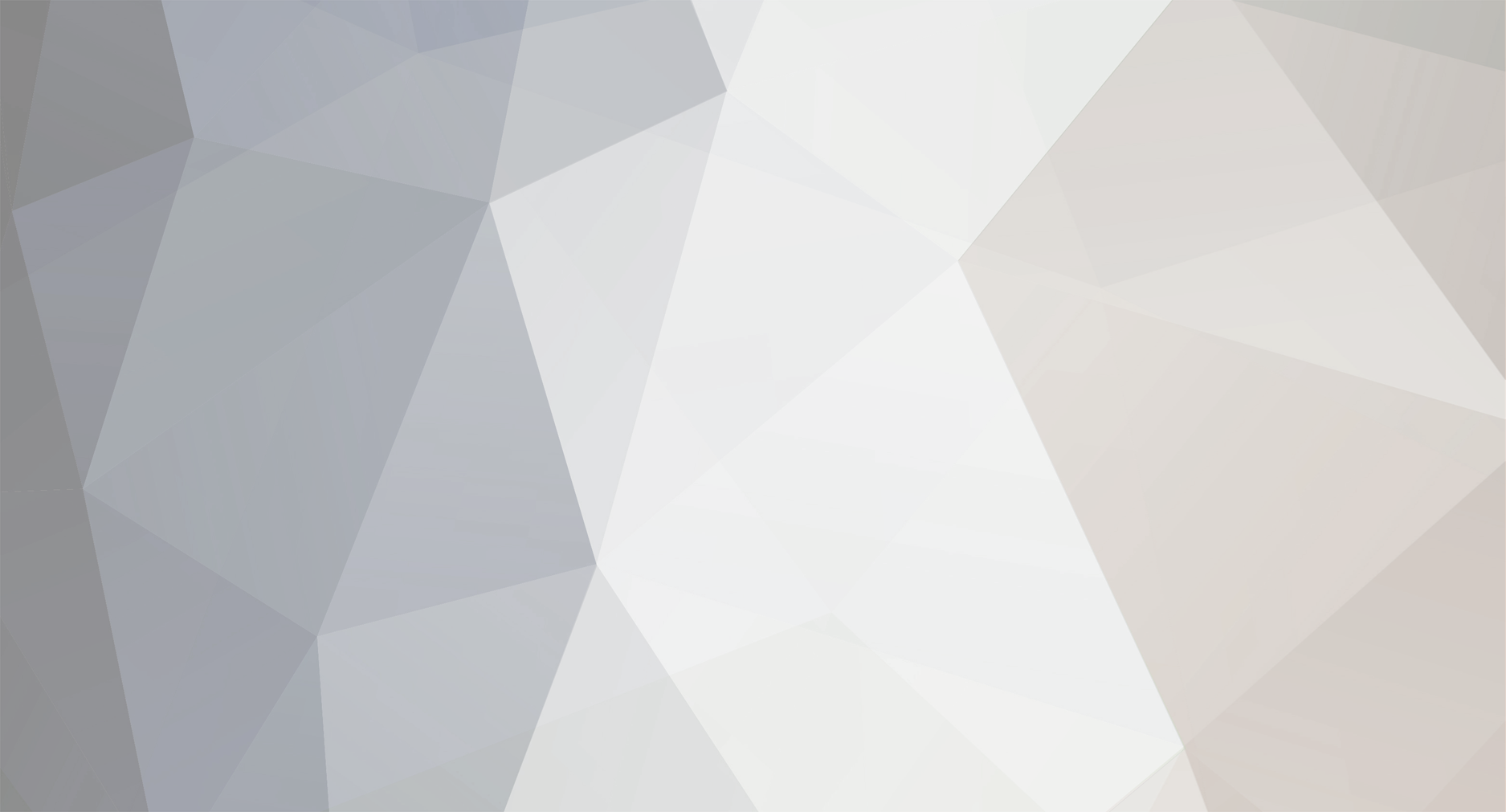
Meinolf
Members-
Posts
169 -
Joined
-
Last visited
-
Days Won
17
Content Type
Profiles
Forums
Events
Gallery
Community Map
Everything posted by Meinolf
-
Hi Docc, here you go: http://www.von-der-salierburg.de/download/GuzziDiag/IAW15xEEPROMTool_V0.04.zip And here's the XDF: http://www.von-der-salierburg.de/download/GuzziDiag/xdf/15M_EEPROM_V1.01.zip Cheers Meinolf
-
Hi Docc, a faster and much more convenient way to set CO trim is using the EEPROM writer/loader from Beard. No need to start the engine and bring it up to heat, also avoids the need to clear the stored errors first. Program and XDF are on Beard's page. Cheers Meinolf
-
Hi, the tach is driven by a square wave signal from the ECU, pin3 on the 15M & RC. Cheers Meinolf
-
Hi, it's about blueprinting the engine. I have yet to see a Guzzi engine where the actual and indicated TDC are identical. Offsets are typically in the range of 1-2°, but I have also seen 4°. That might sound like a minor deviation, but setting the timing right is probably the cheapest and most noticeable tune-up available. And if you are doing it anyway then setting the camshaft wheel so that the lift of the exhaust valve and opening of the intake valve are coinciding at 3° before TDC is the recommended value. I remember that L.Apfelbeck even recommended values of up to 15° for engines with ram rods. I wouldn't modify the dowel plug in the camshaft, but instead drill either a single hole at the necessary offset into the camshaft wheel or bore another 4 holes with 72° degrees offset. That would give you the option to offset the timing by +11.4/-7.6, +3.8/-15.2, +15.2/-3.8, +7.6/-11.4 degrees respectively. On models with ECU (the picture in my previous post is a LM3) I would only correct the timing to factory specs or a slight advance. I don't know where in the ECU code the ignition and injection timing is calculated. Changing the value to more than the 3° before TDC can be compensated for the ignition values by adding the value to the ignition tables, but I don't know where this can be done to the injection values. Cheers Meinolf
-
Hi, the most accurate, and easiest, method to check the TDC mark is using a cylinder stopper and a degree wheel. You don't need a dial indicator for that purpose. Fasten the degree wheel to the rotor and screw the stopper into the spark plug hole. Gently turn CW until the cylinder is stopped and note the degree. Turn CCW until stopped and note the degree. Add the 2 values and divide by 2, that's the TDC. I fabricated a stopper from a spark plug by drilling it through, cutting a thread into the hole and inserting a screw rounded off at the end. Take care not to interfere with the valves. If you want to check the timing of the camshaft, you ideally use two indicators fastened so that you can measure valve lift while turning the camshaft with 0mm valve play set. Take measurements every 2° of crankshaft, note down the valve lifts and determine the point of intersection. That's the one where the two curves intersect in the next picture. https://db.tt/UitlzOqp The best value is intersection 3° (crankshaft) before TDC. If the measured value is off a new hole needs to be bored into the camshaft wheel. Here's a picture of the setup. https://db.tt/gAp4wpUC Cheers Meinolf
-
Hi, What does this mean? re-read my earlier post. The mechanical synchronization with closed throttle is done with both idle stop screws, with open throttle it's done with the white screw on the connecting rod. The 15M/15RC doesn't have this functionality. Later ECUs do. The ECU can neither sense if an adjustment of TPS has been made nor can it be told. It reads the voltage coming from the TPS and uses the according breakpoints in the maps. Assume that, if you have backfiring at constant throttle opening, the engine is running much to lean due to lean map values or a leak on the intake side. If it backfires while closing the throttle, you might have a leak in the exhaust as well. Cheers Meinolf
-
Hi Roy, let me answer in the same sequence. 1. CO and Lambda are equivalent. See the chart here for the values: http://www.mad-d.ch/attachments/063_Umrechung%20Lambda.pdf . So you might go after a CO value of 5.00 using the CO tester or a Lambda value of 0.86 or an AFR of 12.63 using the WBO2, it's all the same. 2. Here it get's a bit more sophisticated. Mixture is one part of the equation, ignition the other. The speed at which the mixture starts burning depends on the AFR. A lean mixture ignites slower than a rich mixture, so the ignition should be changed following the mixture. Normally one wouldn't have the means to determine the best ignition timing in his home workshop or garage, so this part of the equation should be disregarded. Focusing only on the mixture it's really depending on what your targets are. The V11 and Jackal idle well at Lambda up to 0.96-0.97. Anything leaner requires engines which are specifically designed for a >1.0 Lambda ratio and employ very sophisticated technologies. Guzzis aren't. For all intents and purposes any mixture up to 0.97 Lambda is ok, personally I've set 0.92. Some more details here: http://www.cartechbooks.com/media/wysiwyg/9_12.jpg 3. See 1. 4. Well, here in Germany a CO tester is cheaper than a WBO2 sensor and logger. But, the latter one is more versatile. For example in measuring both cylinders and synchronizing the mixture, the ECU has 2 fuel maps, one for each cylinder. And getting these synched gives a real boost plus lower vibrations. 5. Yes. Like we did with the old-style carburetted engines and the idle mixture screws. Adjust CO values upwards until the rpm drops, adjust CO downwards until the rpm drops, select the CO value in the midst. That would be 0.86 or close to it. Cheers Meinolf
-
Hi Gentlemen, looking at above comments makes me wonder if the destination is the same for all... The targets (achievable with this procedure) are: 1) Baseline the TPS and the BIN 2) Remove any mechanical play at idle and the with the throttle open 3) Achieve a stable idle at the desired rpm using the 2 influencing factors at your disposal The steps neccessary to achieve above targets are: 1) Set the TPS to 156mV with the throttle valves fully closed. No more voltage measurements are neccessary after this has been done 2) Sync the cylinders using left and right throttle stop screws with the throttle closed. Sync the cylinders with the throttle opened. It doesn't matter how much opened, as long as the mechanical play is taken out of the equation. 3) Set the desired idle using both bypass screws and both idle stop screws. It doesn't matter (there is no defined target value) how much the bypass screws are opened. It doesn't matter (there is no defined target value) how much the two idle stop screws are turned in. What are the results: 1) The ECU receives the voltage from the TPS (which it translates into degrees of throttle opening) which directs it to use the proper values in the diversity of maps using the TPS setting. These are the fuel maps, the ignition map and a diversity of correction tables 2) The mechanical play of all mechanical parts is taken out of the equation and cylinders are synchronized to work at throttle openings which provide identical power (which is indicated by the same pressure as measured with the sync tool). Less vibrations also. 3) A stable idle at the desired speed. Which factors influence 3): The 2 factors which influence this are air passing through the throttle body and the amount of injected fuel, (Ignition time also does, but that's a separate topic) Air is influenced by throttle opening and bypass opening. Fuel injected is based on fuel map values and setting of CO trim. The relationship of air and fuel is AFR. The best power is at an AFR of 12.64, which means the engine turns over fastest with this mixture. If the engine turns to slow at idle, it can be to lean or to rich. If it's to lean, add more fuel by changing the CO trim. A better way is to change the fuel map value, as this does not influence the mixture at other TPS/rpm points. But you need a WBO2 or a CO tester to measure this. If it's to rich, add more air or decrease fuel. Adding more air is achieved by throttle opening and bypass screws, decreasing fuel by changing the CO trim (and/or fuel map values) If above doesn't result in a stable idle, there's either a fault somewhere (TPS, either of the temperature and barometric sensors, injectors, ....) or the fuel map values are not suited to the specific engine. If you have the inclination, time and required equipment also change the correction tables for air and engine temperature and barometric pressure. The original ones are flawed. This would ensure that the idle remains stable regardless of ambient conditions. Cheers Meinolf
-
Hi, no 156mV is value to set with the butterfly valve fully closed. Which it is only after disconnecting the rods, screwing out the throttle idle screw and unhooking the cable of the idle lever. Cheers Meinolf
-
Hi, that's how you measure. Cheers Meinolf
-
Hi, not really. The CO trim changes injection time. The ECU uses the following formula t = (value x multiplier) x 64.5µs. The multiplier, thats a value stored at $B7B3 in the BIN, extends from 0% to 200% ($0-$FF). Assuming the multiplier value in your BIN is 1 ($80), the CO trim value would be t = (value x 100%) x 64.5µs. Then the following formula can be used to calculate Lambda. λnew = (λcurrent x (base map value + CO trim value)) / base map value But that's theory. In reality you will not know what the base map value is at which the engine is currently running. So you need to measure anyway. Cheers Meinolf
-
Hi Roy, this probably needs some background explanations. The 15M is an alpha-n type ECU. That just means that TPS angle (alpha) and rpm (n) are used to determine breakpoints in tables in which values are stored which translate into the opening time of the injectors, which determines the amount of fuel injected. Plus plenty of correction factors, partly in tables and partly as scalars. The basic equation looks like this: Injection time = (Fuel map value + cold start value) x n correction factors. There's one base map which contains the values for the left cylinder and an offset map, which contains the delta, as plus/minus values, for the right cylinder. At the time the 15M was launched no tools existed to download the content of the ECU (=BIN), which is a mixture of program code and data. In fact the ECU code doesn't even support downloading of its content. Beard, the author of GuzziDiag, devised and used a method to get to the data nevertheless. Which, btw, is the reason why the download of a BIN takes ~15min and uploading only a couple of seconds, Now, as with any device an engine is the sum of components, each of which will have tolerances. Adding the tolerances will result in deviations. Now add external circumstances such as air temp/pressure, quality of the fuel, legal requirements for emissions and noise different from country to country, wear of components over time, and so on. The BIN and its values should cover all of this. It's obvious that such a BIN is not tailor-suited to any specific engine. If the tolerances even out then it might be perfect or close to it, but that's rarely the case. So the vendors needed methods of adjusting the values to a specific bike and found 2 methods, One is CO trim and the other one are the bypass screws, CO is equivalent to AFR. So adjusting the CO trim changes the injection time which influences the AFR. On the 15M this can be done with GuzziDiag. The trim values, the range is -127 to +128, are added to be base map values. At low TPS/rpm the base map values are lower than at high TPS/rpm. Adding 1 (CO trim) to 10 (base value) equals 110%. If the base value is 100 then the percentage change is 101%, That's why changing the CO trim has less impact at higher TPS/rpm settings than at lower ones. The bypass screw has the same effect. But instead of changing the injection duration and thus the amount of fuel it opens a path for air to enter. The main differences are that the CO trim affects both injectors/cylinders, the bypass screw only one cylinder and the CO trim is a quantified change, the bypass screw is not (unless you take # of turns as precise quantity) The instrument used for measuring can be a CO tester, I use a AFR logger from Innovate, the LM-2. As the CO trim changes the injection duration of both injectors measuring CO at the tailpipe is ok. On the 15M the CO trim can be changed with GuzziDiag and other programs, As to the value to aim for, that's an interesting question. What do you want to achieve? If it's just the value required by law, take that. Otherwise it get's a bit more complicated. There are some basic correlations between λ, power, emissions and efficiency. Bypassing the emissions, a λ of 0.86 gives best power, a λ of 1.05 gives best efficiency, I have BINs where I targeted λ 0.88 in all areas, that is all of the 256 breakpoints I could reach while logging, and others which are more sophisticated. See here https://db.tt/zptc3hQB The Guzzi engines, in my experience, idles well at any λ from 0.7-0.98. Cheers Meinolf
-
Hi Docc, the thought is correct, AFR will be impacted. But whether the result is a rich or leaner mixture depends on the actual values in the fuel map. I found that Guzzis are very forgiving in regards to rich mixture. During my experiments I had extended areas where Lambda was at 06.-0.7. I didn't feel it when riding. Lean conditions, on the other side, are very much noticeable. Any time Lambda exceeds 1.0 the bike gets jumpy. In this case using the CO trim setting would be the prefered - but not best - approach. The CO trim adds a constant value to the injection time, whose influence will be biggest at low fuel values and decrease with bigger fuel values. The best approach is to measure AFR and adjust the fuel values to achieve the desired AFR. Cheers Meinolf
-
Hi, and again I completely agree. It's a small difference, and the resolution of the AD makes it seem even smaller and less important. And who knows the the accuracy of the AD? And not everybody will be using a hi-quality DMM to measure and set the voltage. And the TPS tends to slip a bit when fastening the screws. And.... BUT, why not use the value we know to be correct and try to get as close as possible? Cheers Meinolf
-
Hi, it's not really according to Meinolf, but according to the curve of the TPS used, PF03C. The formula of the PF03C for voltage dependent on opening is mV = (degree x 105) / 150. If this is changed to Degree = (mV-150) /105, it's easy to see that the calculated degree value will be As the voltage resolution of the 8bit AD is 0.01953V (5V/256), the first voltage value step bigger than 150mV is the 8th (8 x 0,01953 = 0.15624V). So the cell $07 contains 0 degrees as value, the cell $08 0.06 degrees and so on. So this is were the 156mV come from. As the values in the original TPS lookup table, in all the BINs I have seen, are slightly off, here's a recalculated and correct one (for PF03C): https://db.tt/bhegzYG1 Cheers Meinolf
-
Hi, the right and left hand idle stop screws are used to adjust the idle speed and synch the cylinders at idle after the TPS base setting was done. You don't need GuzziDiag to adjust the TPS. The granularity of the 8bit AD in the ECU is not good enough to use GuzziDiag to set the voltage to 156mV. A DMM is needed for the purpose. Cheers Meinolf
-
Hi, I fully agree. The adjustment procedure using the bypass screws stems from the time when the BIN couldn't be modified. The best approach is to keep the bypass screws completely closed and adjust the mixture by changing the values in both fuel maps based on logged data. Which has the beneficial side effect of making good BINs transportable to other bikes as the unquantifiable influence of the bypass screws is avoided. Yes, that's my SOP when checking the synchronization after having made significant changes to the BIN. It's a bit awkward, but can be done if the road is empty and straight. It's 156mV, not 150mV. That's a 4% difference and you do feel the effect. The air flow at low throttle openings is a very turbulent one and getting the mixture right and stable at low throttle settings is really time consuming. I've spent 50% or more of the entire logging focusing on the 5% breakpoints at low rpm and TPS opening. Again, completely agree. I found an idle of 900rpm with a completely cold engine right after starting, which increases to a rock-solid 1000rpm at any other air or engine temperature to be high enough to provide sufficient oil pressure even if the engine is cooking and also charge the battery sufficiently. To increase engine breaking I also added fuel cut-off at the lowest three TPS break point columns down to 2700rpm. Which is not essential for the Jackal, but very helpful with the V11 if driven spiritedly. Cheers Meinolf
-
Hi, for some time now I have been looking into the function of the 15M ECU. Over time this expanded to sensors, actuators and other peripherals having impact on the gas flow and mixture and then more and more deep dives into the theoretical background.The 15M has lots of potential, even though it's quite simple compared to the current generation of ECUs. My initial approach was to change the fuel maps based on road data logged with a LM-2. But that quickly turned out to be a short-sighted one, as this is just scratching the surface. So I built this ECU simulator https://db.tt/G7pXsKEx and started a systematic research, trying to reverse engineer the unknown functions of the multitude of tables and scalars in the ECU code. All of the findings are applied to the BINs I use for road testing and logging in my V11 and now a Jackal as well. I have also shared my BINs with several members here and on Wildguzzi, the general feedback was good even though BINs optimized for a specific bike leave much less room for deviations than the original BINs. In short, the findings so far are that all! trim tables in the BIN identified so far are lacking. Neither air nor engine temperature or the barometric correction were correct and the TPS look-up table contains wrong values. The impact of the individual settings on AFR is usually quite small, but errors add up. So one percent here and two percent there can add up to the mixture being off by 10 or 20 percent in the end, and that's noticeable. As many have experienced yourself, looking at the problems reported here. So a laid back approach to getting the base settings right, replacing sensors with resistors, changing the CO trim or twiddling the bypass screws results in just that, a laid back performance. Cheers Meinolf
-
Hi, then you are making a mistake. Setting the TPS to 156mV (not 150mV) with all rods disconnected and both throttle stops fully out is key. The ECU code contains a 16x16 lookup table, which converts the voltage coming from the TPS to degrees. The cell $08 in the lookup table contains the 0 degrees, the voltage corresponding to that opening is 156mV. If you don't get this right then all values depending on the TPS opening (fuel, acceleration, ignition,...) will be off target and the ECUs uses the wrong values. That is, values don't match to the actual opening. That is most noticeable at low openings, because the free cross sectional area of the intake increases following a cosine function. That means that a low openings, say going from 1° to 2°, a small change results in a much bigger free area changes than at large openings. Below is a sample calculation for a Jackal, which has a smaller bore than the V11, but the relationship respectively the %-changes are the same. TPS angle alpha (break points) Athrottlevalve Cross section area of throttle valve [mm^2] Aflow Cross section (Throttle body - Throttle valve) [mm^2] open cross section (Throttle body - Throttle valve) % change versus previous TPS break point 1 1235 22 1,7% 2 1213 44 3,5% 50% 4,05 1168 89 7,1% 49% 4,6 1156 101 8,0% 88% 5,33 1140 117 9,3% 86% 6,3 1119 138 11,0% 85% 7,54 1092 165 13,1% 84% 9,01 1060 197 15,7% 84% 10,85 1020 237 18,8% 83% 13,43 965 292 23,2% 81% 16,93 891 366 29,1% 80% 21,53 795 461 36,7% 79% 28,15 664 593 47,2% 78% 37,03 500 757 60,2% 78% 48,28 319 938 74,6% 81% 60,93 158 1098 87,4% 85% 84,8 267 989 78,7% 111% 90 262 995 79,2% 99% Hm, the paste and copy of the above table didn't work. A simple formula to calculate the cross sectional area is: A = (3.14 x D2 / 4) x (1- (cos alpha / cos alpha0)), where alpha is the opening angle and alpha0 is the angle with the butterfly closed. If you are interested, here: http://www.diva-portal.org/smash/get/diva2:23184/fulltext01is one source for the calculation. Page 13, 3.1.2. The opening at idle is not critical. It will be what results out of setting the required idle speed with both cylinders synchronized carefully. Cheers Meinolf
-
Hi, and if you have AFR logging at your disposal, then go the full stretch and use the corrected trim tables I have published elsewhere for engine temperature, air temperature and barometric pressure. Else you will be tuning the fuel map values to one specific situation ONLY. AFR will change significantly overall and differently between cylinders if this is not done. Also change the TPS breakpoints, at least the smallest one, to coincide with the actual TPS setting at idle. My recommendation is to change several others (in the range of 6-13°) as well. The ones I am using are 0.99, 3.31, 4.23, 5.15, 6.44, 7.54, 9.38, 10.85, 13.43, 16.93, 21.53, 28.15, 37,03, 48.28, 60.93, 84.84. 0.99° is the TPS setting at idle speed on my bike. Which, with syncing via throttle stops (at idle) and correct fuel values at that break point results in an idle of 900rpm after start (cold engine) and a rock-steady 1000rpm at any temperature once warmed up. The Lambda I have choosen as target (and set) at idle is 0.92 and identical for both cylinders. The results are worth the effort. And make BINs much more interchangeable between different bikes with the same set-up. Cheers Meinolf
-
Hi, the following explains why the adjustment procedure including TPS setting is the way it is. The ECU only sees what is send to it by external sensors. These are the TPS (and several others). TPS only provides data about the right throttle valve. The ECU code contains several tables which provide the translation from voltage to degrees (in case of the TPS). The value for fully closed throttle in this table is 157mV (not 150mV). So that's the value you set the TPS to when everything is disconnected. The value after reconnecting the linkage doesn't have to be 525mV. It can be 500 or 400mV. The ECU will interpolate anyway (unless you follow below procedure, then your idle setting is exactly at a break point). Set it so the specific bike idles best. The 8bit A/D of the ECU sees voltage in steps of 0.0195V. If the TPS base line is set wrong, the ECU sees the opening of the throttle different from where it actually is. This means that values from a different break points are used in the multitude of tables it uses to select and calculate injection duration, ignition, .... The rest of the sync procedure just aligns the left cylinder to the right. IF you have the means to measure AFR then forget the fiddling with the bypass screws. Close both completely, sync and set idle speed with both throttle stops (left and right) and set the right mixture at the break points in the BIN. This eliminates the random flow of air thru the bypass screws at idle (and to a lesser degree at higher rpm). If perfection and transportability of a BIN between different bikes is the target, then the CO trim should be at 0. Cheers Meinolf
-
Hi Hubert, properly speaking, no, I'm not sure about the improved laminar flow. I normally try to stay within the bounds of my knowledge, this was an guesstimate and not a fact. Cheers Meinolf
-
Hi Luhbo, the plain german statement is here: http://www.guzzi-forum.de/Forum/index.php?topic=30093.0 For those not fluent in German. I was interested in the effect of the snorkels on the volumetrics of the engine and the impact the snorkels might have on the intake air temperature, so I measured AFR and air temp with and without them. The finding was that the engine run leaner to the tune of 1-6%. As the injection values were constant, the leanness resulted from more air moving through the engine at the breakpoints where I measured. The air temp didn't show any significant changes. When analyzing the logged data I also found that the fluctuations of the Lambda values went down from an average of +/- 0.25 to +/-0.08 (That is a factor of 3, and not of 4, as wrongly stated in my previous message. I'm not good at arithmetics). Which, to voice an opinion, indicates a much more laminar airflow with the snorkels than without. The summary is that well shaped air inlets, even if the diameter of the inlets is smaller (than the inlet in the airbox), are more efficient than sharp corners. Which is not a new revelation, but a long established fact. So, if one wants to do sound tuning, remove the snorkels. If one wants a more efficient system, keep or add them. Cheers Meinolf
-
Hi, I agree with the first point, but my measurements indicate differently on the 2nd one. When measuring air throughput with and without snorkels I found that it increases 1-6%. And air Lambda fluctuations decreased by a factor of 4 3. My impression was that the engine ran significantly smoother. Cheers Meinolf