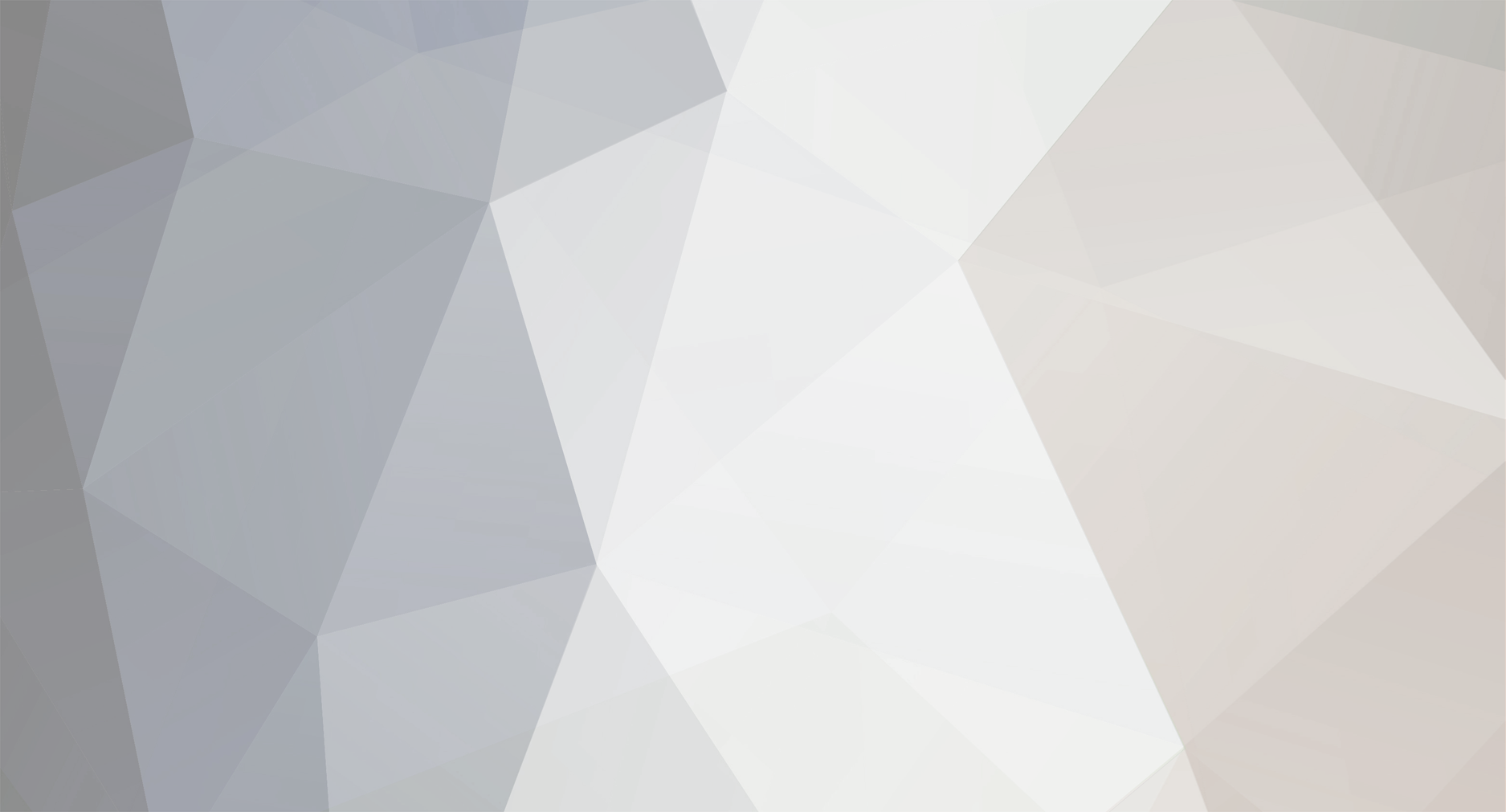
dlaing
Members-
Posts
7,096 -
Joined
-
Last visited
Content Type
Profiles
Forums
Events
Gallery
Community Map
Everything posted by dlaing
-
Excellent point about the inertia. Yes, I would agree that if the engine is rev'd up up high enough and clutch is dumped the clutch might slip or the rear wheel MIGHT slip before and or while raising the front end, the clutch would more likely slip in higher gears. I hope that is not the real world way that people treat their Guzzi, but if so, you are correct. But you are not correct about infinite torque, although the torque could be large enough to break the driveline, but assuming by no elasticity you mean it is also unbreakable and the only give is the cush and the rising of the front wheel, you still could not reach infinity even with one of them 600HP Hayabusas and a one ton fly wheel. Dumping the clutch might be equivalent to shooting a cannon at a torque wrench with deflection equal to that of the cush rubbers when the wrench is metering its maximum of One Trillion foot pounds, with the torque wrench hooked to the axle in such a way that it turns the wheel. It won't reach even One Trillion foot pounds. Maybe a patriot missile might reach a trillion foot pounds. Infinity is a much larger number than what is relevant here. Still you made an excellent point that the impact force can be far higher than steady engine acceleration, and that the clutch or tire traction could give before the front wheel rises and if the force is high enough the clutch or tire friction will surely give before the front end rises. This reinforces the potential benefits of a bushing that could better absorb the impact of a dumped clutch!!!!!
-
Whether you drilled or not, there is no need for shame. Some Guzzis run with no cush, so unless you drilled the "rubber baby buggy bumpers" to the point of imminent deterioration, you still got cush.
-
So, here is a recap: The big hole I missed was the Center of Gravity. But it was not caught by Ratchet, whose math or physics was off by over ten fold. And then I came up with a second theory/question. To which Ratchet replied Thankfully, Troy came up with the CG factor that I had completely missed: And Ryland added with great clarity that even a gerbil with a high school diploma can understand: Which is all excellent, but I disagree that "the peak torque on the rubber baby buggy bumpers is limited by the dynamic frictional torque the clutch can transfer, or the static frictional force of the contact patch" In acceleration mode it is limited by the front wheel lifting and in deceleration mode, it is limited by the frictional force of the contact patch. "rubber baby buggy bumpers" Very nice!
-
Tuber or not tuber
dlaing replied to belfastguzzi's topic in Special place for banter and conversation
Finally a thread with the correct answer to the question! -
Antonio currently has an ad for Ohlins forks in Classifieds: "Standard fork for the V11. price 1000,- Eur Shipping not included " http://www.v11lemans.com/forums/index.php?showtopic=12846
-
Huh!?! I thought you were talking about the 95mm pistons and cylinders from the 1200S and Norge 1200. Who made these cylinders?
-
Did you get your name, Hairy Cannonball, from your expertise with gerbils? Finally an expert worthy of answering my questions!!!! Do you use muscle relaxants? How do you get them out? Have you ever had rabies? Do you think when you die you will be reincarinated into a gerbil used for some idiot's pleasure? Can intellectual pursuits in engineering be degraded even further?
-
There is also the possibility that your new cable was not inserted correctly at the engine. If inserted incorrectly, the tip of the cable rides on the top of where it is meant to fit, allowing enough friction to turn the speedo for about ten miles, or so... The side effect of not fitting the cable correctly is that once tightened down it MIGHT now be pushing the assembly above the engine apart. If this is happening, no worries, it can simply be pressed back into position, reassembled correctly, and then many happy miles of legal obedience to the speed limit are possible.
-
SMOKED A V-ROD THIS WEEKEND
dlaing replied to mason's topic in Special place for banter and conversation
Not political? Yah, and I'll bet you never inhale -
If the main point of the cush is to protect the drive line, you would want to engineer the cush to absorb as much of the damaging energy as possible so that it is not transmitted to the splines, etc. You can graph the deflection against force and show exactly how the splines are being protected. If you only get a millimeter of deflection when you go from 50 to 60 foot pounds of ENGINE torque while in first gear, it will indicate that your drive line is not well protected when you hit the gas hard enough to lift the front wheel. If what you say is true that you will get a rising rate until the holes close and then a steep transition, it is the steep transition and especially the end of the transition where the worst damage is likely to occur. Ideally we want the bushings to deflect as much as possible as we approach maximum force. The suspension analogy is that drilling the rubbers is like going with a softer spring. In general, the more you soften the springs, the smoother the ride will be over small bumps, but the large bumps will more likely cause the suspension to bottom out. The bottoming out is potentially the most damaging. If protecting the riders kidneys is the objective, the ideal spring for most bikes will be as soft as possible without bottoming out. The same holds true for cush bushing design. Where the analogy breaks down is that a rider will feel the greatest comfort with the ideal spring if they ride over various terrain, but the rider won't feel the bottoming out of an over-drilled bushing. They will only feel the smoothness of the less threatening impacts on the drive line. You appear to bee attempting to use your common sense to suggest that no protection from the maximum impacts is lost. You may be correct, but you might not be. My common sense, and my obsevervation of how soft the rubber is leads me to believe that the bushings may in fact be too soft, in the direction of accelleration. Maybe Guzzi bushings come in inconsitent levels of softness??? I certainly would not call mine "chrome-moly" hard. Increased progressiveness would probably be a good thing, and drilling can increase progressiveness, but maintaining adequate firmness to prevent bottoming should be the number one design criteria. Without testing, the ideal softness of the bushing is unknown. Observations of smoother driveline have value, but the drilling may be compromising the life of the driveline. Probably not a big deal when most V11s will be junked before they reach 100,000 miles. I am just defending the premise that a better bushing could be made.
-
It all started with claims of chrome-moly hard rubber and a needless rejection of the idea of using urethane. This thread had the usual rudeness of the usual suspects. Shameful. I am just waiting for Ratchet to admit that he was wrong about rear axle torque.
-
If you want to wait another six months, hook the computer up to the plasma.
-
What do you mean, "from all the accounts"? I don't think more than one person, if even one, said it was "wrong". I suggested that it could be improved on and that the added smoothness makes a compromise giving a vaguer since of engine response and that it might shorten the life of your splines if it turns out it is "bottoming out". But that does not mean it is "wrong" any more than putting a hose clamp on your oil filter, or spending money on a windage plate or spend money on high compression pistons, or optimizing the fuel map beyond that of a downloaded map is "wrong". If anyone said anything was "wrong" it was those that suggested urethane wedges were wrong!
-
Do you have plans for the rear shock? I would guess you would need at least a 600#/in spring, Maybe a 650#/in.
-
Thanks Troy! That fills in a couple of major missing pieces. Now that I think about it, of course you need to consider center of gravity and wheel diameter. Ratchet probably knows the front wheel weight. Center of Gravity would be very difficult to calculate. I would guess it is a little lower than 2 ft. We would want to assume a full tank of fuel, since we are looking for the maximum number. But I think the result should be just a little more than 705ft-lb. Maybe claims of throttle wheelies from the more powerful V11s is not as exaggerated as I had thought. The best dyno charts posted here show about 75 foot pounds of torque, but I suspect that is from overly generous dynos, and typically with simple modifications people are getting about 65 foot pounds. I think designing the wedges to "bottom out" at about 70 ft-lbs of engine torque would be ideal. 70 ft-lbs times 11.7589 equals 823.123 and 823 divided by six cushes equals 137. So, if the wedge could be designed to produce a nice progressive curve, "bottoming out" at about 137 foot pounds, I think we would have an ideal product. But I would not be surprised if the OEM wedges are already close to that. Someday I may rig up a way to test the wedges. If I can just find a socket that fits the splines and won't strip them at 137 foot pounds of torque....
-
No, I don't think it would not result in damping or dampening. In fact it might transmit more of the fluctuations that we might want to dampen. I think having a fine orifice dampen the oscillation would be more beneficial, than the very slight delay that it would cause. How much would it delay it, maybe one firing cycle at high rpms???? The delay probably would not be noticeable. With my TwinMax I added extra restrictors (infinitely adjustable plastic things) to dampen it even more than the stock brass fittings. I never noticed any delay in response to throttle changes.
-
I don't know how you handle the stress! I only lost a few dollars by not showing up for the last San Diego Rally, but this is more of an investment. But it is nothing compared to what you have sunk into the rally. I can't imagine how much you personally have invested with no guarantee of breaking even, and no potential reward other than an attaboy. Thank you for all you do for our community. I'll post the question over at the SoCal web board.
-
You stole my idea!!!!! Just kidding, Your idea certainly is not swiss cheese overkill. My idea was very different and even more minimal in effect, so much so that it did not make a noticeable improvement. I did one single drilling from the outside of the pie towards but not all the way to the tip of the triangle. Something like this with drill hole in red | ..\\ | ........\\ | ..................\\ | ............................\\ |...........................................\\ ===================:::::> |...........................................// | .............................// |...................// |..........// | ..// Is that abstract enough? The genius theory behind it is that as the wedge is pushed toward the the outer wall, it seals the hole, and then as the wedge is squashed, the cavity retains air and acts as an air cushion. FWIW I only did it to the decelerating wedges. Patent Pending....
-
I thought that was a picture of hakarl (buried shark) http://en.wikipedia.org/wiki/H%C3%A1karl The lutefisk jokes at wikipedia are amusing... "When Lutefisk is Outlawed, Only Outlaws Will Have Lutefisk! " http://en.wikipedia.org/wiki/Lutefisk
-
A good solution would be to use hose with a smaller Inner Diameter. Maybe it would be helpful to only use the right cylinder for vacuum reference??? I don't see any drawback.
-
Thanks for making the effort! All I am interested is the torque at the rear axle divided by the number of bushings. So, your answer of 65foot pound maximum is about what I expected from you based on your earlier reply. So, I shall stick to the idea that your math is wrong. Technically you make a good point about the actual force on the bushing. It is not torque. But I don't need to know the exact force at each bushing. All I need to know is how much torque is generated at the axle. The torque can then be reapplied in a test environment with the bushing the same distance from the center of the axle. Once I know what the torque is, I can take a torque wrench and fit it to the splines (not trivial), insert one bushing into the cush housing(or maybe two for balance) and turn the torque wrench measuring the compression of the bushing at various points of applied torque. Given your 65 foot pounds of maximum force, the deflection of a full set of bushings would be pretty minimal. This is where we don't see eye to eye, and I believe the force can get up to about 1250 foot pounds of force at the rear axle when popping a wheelie. It is not irrelevant. If I apply WOT in first gear at 3000 RPM and hold it up to about redline, my front wheel does not lift unless I hit a bump in the road. However if I pop the throttle at about the point of maximum torque, I can exceed maximum torque as I get added force from the momentum of the driveline as it un-slackens. Likewise popping the clutch can help exceed the rated engine torque applied to the rear wheel. Yes, once the front wheel is up in the air, I imagine there is no significant torque. I am concerned with the torque that got it up, not what keeps it up. An interesting academic exercise, but I am just looking torque at the rear axle. Sorry I did not make that clear earlier. Interesting, but way over my head. I would have pursued physics or engineering but I was too undisciplined. I wish the Mechanical Engineers would speak up, but we may have bored them away by not fighting over unmentionables. But no calculus is necessary. We just need to know how much torque at the rear axle is required to lift the front wheel. I believe the torque at the rear axle is greater in lower gears. This is why it is easiest to wheelie in first gear. Sincere thanks for giving it a shot. That is certainly something I like about you. You don't back down from something just because it requires you to read, research, or use the ol' grey matter!
-
But other than the manual there is no evidence of a production V11 being hooked up that way. I have done more than a little research. All I am asking for is someone to speak up who had their bike come from the factory set up that way. I don't think anyone has, unless their dealer was trying to be extra clever with the bike setup. Comments like this tend to lead us into believing that SOME bikes were set up that way from the factory: I suspect it is misleading, and that no bikes were set up this way from the factory, except for maybe some 1999 Europe only models. I certainly could be wrong, and that is why I ask. Yes, I have searched for the answer, but I can't find evidence and the more I don't find, the more I believe that not bikes were delivered that way.
-
So, is the logic beyond our capability? I'll stick to my 705 and 1250 foot pounds of torque until proven otherwise. This may be worth pursuing. A few hundred dollars in R&D to sell a few sets of rubbers that only the truly blessed can understand the benefits of. Maybe I could prove to myself exactly how many holes it takes to optimize the OEM rubbers for 1250 foot pounds of torque? Assuming they are not already optimized for less torque?
-
I already did. I have quite probably put a major hole in the drilled cush rubber bushing theory. With one of my formulas for popping a wheelie, we get 1250 foot pounds of torque at the axle. With the dyno measured engine torque applied to the gear ratios I get 705 foot pounds of torque. But you never really offered any math, just your usual hyperbole and sarcastic approval of my math. Ratchet, please answer these questions: Approximately how much torque is each acceleration bushing enduring when one pops a wheelie? Approximately how much torque is at the rear axle for our bikes when in first gear if the engine puts out 60 foot pounds of torque? And please show the math you used to arrive at the answers. The splines are quite likely more prone to damage after drilling the cush rubber bushings. But to prove it, we might need to set up a jig to apply 1250 foot pounds of force, divided by six bushings....assuming that the 1250 foot pounds of torque is about the maximum pressure that the six acceleration bushings would have to endure. Then again, maybe it is not that big a deal for it to "bottom out" at wheelie popping torque. Perhaps if it bottoms out at only 600 foot pounds or so, it has already protected the splines from nearly half the 1250 foot pound force, and maximum torque can be delivered more efficiently????? Is the lost protection of the splines worth trading for perceived smoothness (vagueness)? What really concerns me is the people chucking out half the bushings and drilling the other half.
-
Is the dyno measuring the torque the 60 foot pounds at the axle? I don't think so. That would mean that if put a little more than 60 pound bag of cement on a foot long lever coming off the rear axle, that front end of the bike would lift the bike into the air!!!! Something is wrong with your math. But, assuming you are correct that there is only 60 foot pounds of force(plus a little from momentary bursts of a popped clutch), I don't see how that could effect the massive splines, and I don't think we need any cush unless it is not torque that is threatening our splines, but rather vibration eating at the splines and the whole purpose of the cush is to dampen the vibration, not absorb the force of the rather miniscule 60 foot pounds of axle torque. If that is the case we should be looking an elastomer with excellent vibration suppression. But I think your math is off. I think that while the dyno is measuring RWHP, it is not measuring axle torque. The measured torque is probably an estimate of the torque at the crank. Geared down to first gear where we can pop a wheelie that torque is multiplied. But how much? Can we simply use the ratios from the owner's manual? first gear is 1:11.7589 (engine-wheel) So, 60 foot pounds would be multiplied by 11.7589 to give us 705.534. I know my bike with roughly 60 foot pounds of torque can't lift the front wheel without a bit of coercion. How much more torque can we get by popping the clutch? We know it is enough to bring the front wheel up, and I know that my bike won't wheelie from simply giving it 705 foot pounds of torque at the rear axle. It does seem unlikely that we would have to escalate the force from 705 to 1250 just to make the front wheel come off the ground. Assuming my 1250 number is correct, that would correspond to 106 foot pound of engine torque following the owner's manual's 11.7589 ratio. That does seem a bit high. The true force to lift the front wheel is probably somewhere between 1250 and 705 foot pounds.