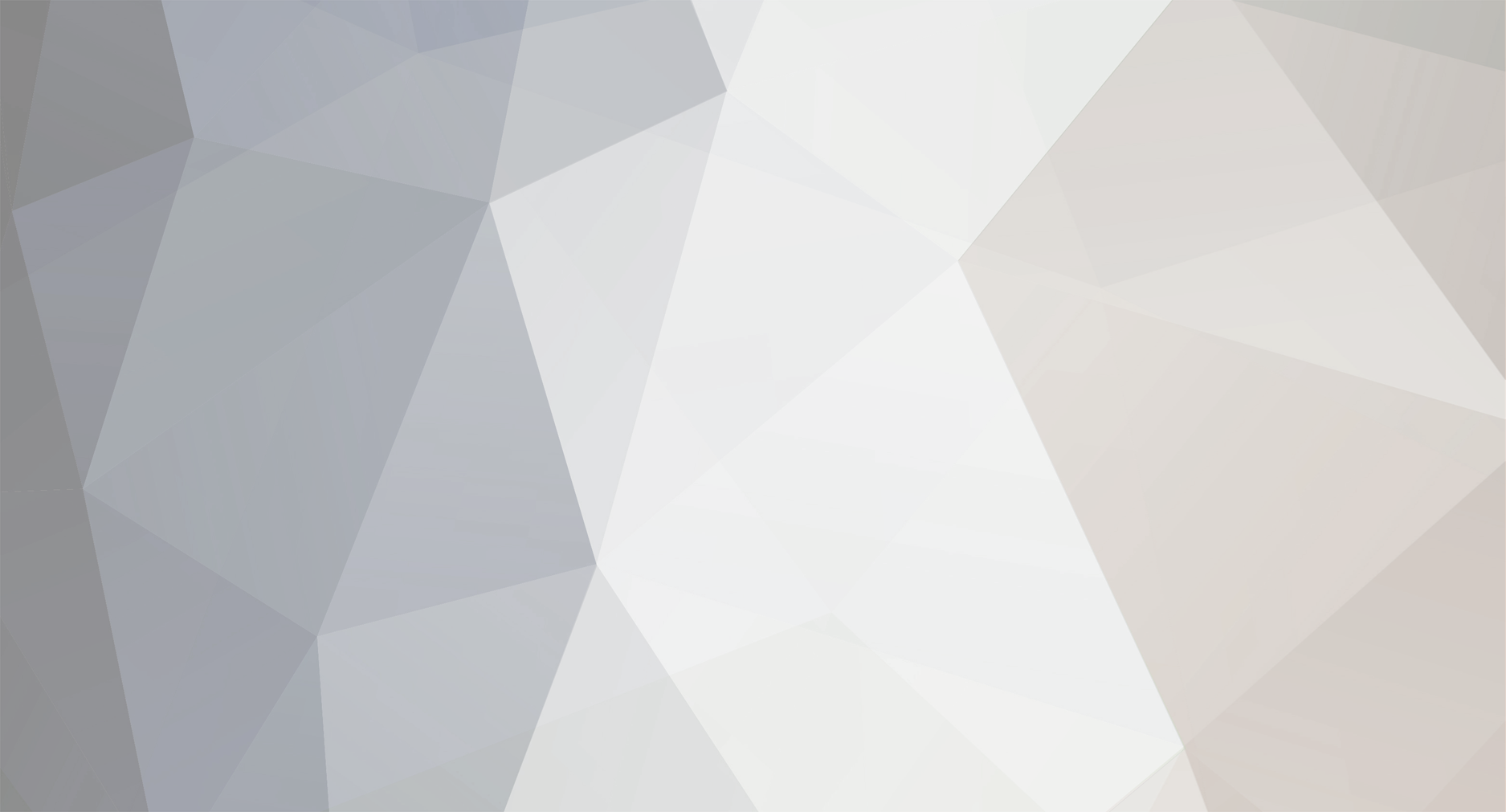
dlaing
Members-
Posts
7,096 -
Joined
-
Last visited
Content Type
Profiles
Forums
Events
Gallery
Community Map
Everything posted by dlaing
-
If the horn and brake light are also dead, look to relays. If not, look to ground at tachometer body.
-
I implied that that might indicate bad diodes, but really it could mean bad other things, and probably is something else if both regulators produce same symptom. I'd suspect the charging line that Greg mentioned, or the regulator's ground, etc.
-
Could this constant on state of warning lights on, POSSIBLY be caused by toasted diodes in regulator???? This might explain charging light, but not oil light???? Easy test is to pull the 30amp fuse. If the ignition switch (or relay, theoretically, but unlikely) is somehow stuck in a bridged on position, this could have significantly reduced your battery's state of charge, maybe not so much that you can't start, but enough that it puts a drain on the charging system. If discharged, the battery acts like a black hole, sucking every electrode it can away from your charging system!!!! The voltage regulator regulates voltage, not amperage, so when the battery is low, more amps than the wiring can handle may occur, and seems to have occurred in your situation. Also, more amps than can be handled by the voltage regulator and alternator can occur, and probably did occur, since you saw 17 Volts. You should charge your battery. If you pull the 30amp fuse and the warning lights are still on,we can assume that the voltage regulator's diodes aren't the cause of the charging warning light on, when ignition is off. Once the diodes are eliminated as the culprit, fix the ignition switch, following Ratchethack's advice. Make sure this fixes the constant warning light issue, if not, look to relays??? In any case, bypass the relay to an external one, following Greg's advice. (I am pretty sure I could have saved myself from buying a new regulator if I had known to do that!!!) Charge the battery, start up and IMMEDIATELY check that the charging voltage is within spec. If not, turn the engine off immediately, and look elsewhere, and report back Best of luck.
-
I googled and found 128 mm stated for the rear for both Ohlins and Sachs equipped bikes, but I know that they should not be the same. The Ohlins bikes have about 2 cm more rear travel (~1cm more stroke at shock) My shop and owner's manual showed nothing. The sales brochure for my 2000 V11S shows a White Power shock with 64mm stroke (which is about 128mm travel) But the shock is a Sachs, not a White Power, and I did a rough measurement on the Sachs and got 60mm. The V1100Sporti was equipped with White Power and its manual diagrams the WP shock as have 64 mm stroke. The Ohlins after market shock is 70mm stroke.(which should provide about 140mm travel (bumper fully compressed)) I am pretty sure the aftermarket and OEM shock are the same, but the same is not true of aftermarket and OEM forks.
-
That's even worse than my weakly modified joke! and funnier, but a lie, because when Michael went to confession, Michael told the priest his confession and the priest relayed to God, saying Michael said he wanted to live a long life and have at least fifty nine years old. God thought for a second, and figured out for himself and confirmed in the book of Truth what Michael really said and meant, so God told the Angel of Justice to make sure Michael did not even have fifty one year olds, and the Angel old and hard of hearing, made sure Michael did not even see 51 years old. Sorry, that may have been even lousier. Back to the topic, Long Live Guzzi!!! Anybody got any facts? How about speculation disguised as facts? Man I wish I could win a super lotto jackpot and buy the Guzzi name, patents, and factory. Any Benevolent Billionaires on the forum??? How about Malevolent Ponsi scheme experts???
-
Ed McMahon goes to heaven, where St. Johnny Carson aka God, grants him one wish. Ed says, "Please kill Farrah Fawcett so I can finally get in her pants" God sends the Jordache Jeans to be hot pressed in hell, Ed is sent there too. Farrah Fawcett goes to the gates of heaven. Before entering, God grants her one wish. Farrah says, "God, life can be so cruel, please save the children, let them be safe from harm." God kills Michael Jackson, and lets Farrah into heaven. Michael Jackson goes to heaven's gates. God grants him one wish. Michael says, "I want to live for eternity like an Italian diva in a castle overlooking the most beautiful lake in all of Europe"
-
Sorry, I just noticed that Guzzitech link is regarding Breva/Norge, so the results could vary from a V11 spine. Also, Todd's review could be construed as biased, but he is a straight forward honest guy, and he chooses products to sell primarily because of the product's quality.
-
Guzzitech has sold a few of the YSS dual shocks for Tonti framed Guzzis and the word is that people have been very happy with them. Here is a link to what might someday be a review of the Mono shock: http://forum.guzzitech.com/index.php?optio...43&catid=43 FWIW, I went with the Penske over the Wilbers, or HyperPro, because the shorter Penske body allowed for more travel within the range of swing arm movement and ideal ride height. And I chose the Penske over the Ohlins because of the alleged tendency for Ohlins seals to leak. (My Ohlins fork seals are doing great!) Also, Penske appears to be Number 1 for service and parts availability. I also pursued White Power Shocks and Elka, but both were dead ends. I don't think the YSS were available when I bought the Penske. If maximized rear wheel travel is not important to you and a slightly higher than stock ride height is good for you, I'll bet the YSS are a great deal!
-
And properly means such that torquing does not increase bearing friction. If it does, then you need a longer bearing spacer. I don't think bearing spacer length is a problem at the front wheel, but some had too short of a spacer at the rear, causing binding at the bearings and bearing failure.
-
Cool question! Some things that can be done are frame bracing. Later V11s have alot more bracing and thus are more stable, but possibly less "fun" Also later V11s have slightly different geometry. If your objective is better handling and money ( within reason ) is no object, then you might consider custom pork chops to move the swing arm axis more inline with the U-joint access. This will shorten the wheel base significantly, making the heavy bike more nimble. You would have to shorten the shaft for this to work. Negatives are increased rear weight bias, more torque effect on shaft, possibly worse foot peg ergos, and less comfort over bumps, which are presumably reasons Guzzi went in the other direction. Forum member Paul M. did something similar to his bike, not a V11...He can better explain the positive reasons for the mod. A sharper steering angle should make it more nimble. I think there may be a bearing kit that steepens the angle. Shedding weight, especially unsprung weight will help. Wheels are the easiest place to make big gains, but why stop there? Battery location could be moved to just behind front wheel, if you go with a smaller battery or pair of batteries. Rear sub-frame could go on a diet, especially if rear seating is eliminated. Drilling cush drive allegedly makes for smoother reaction to throttle input. Obviously improvements to spring rate and damping can be made. I went with Olins forks and Penske shock, but there are many options. I think Guzzi did a fine job, but should have specified lighter wheels and firmer springs.
-
Sorry, but YOU will have to endure. You asked for one simple statement. The trouble with simplicity is that it does not cover all scenarios. If you actually read the full post you would realize you and Dan were excluded from the WE, because it was conditional to having a rich running bike or a willingness to remap to work with the increased conductivity. It must frustrate the hell out of you that I understand thermodynamics better than you. I have congratulated you and Dan for a fine design and improvement on the OEM, but your theory on it is broken. There is room for improvement beyond your design and Dan's large air gap is questionable. You bury your head in the sand and go lah lah lah lah, avoiding The Truth. Keep those square wheels spinning dude. The thermo-paste increases heat capacity, it does not provide low heat capacity. We want high conductivity between the cylinder head and the thermistor, so that thermistor quickly and accurately reflects the temperature of the cylinder head. We want low heat capacity around the thermistor so that the thermistor can quickly follow the temperature of the cylinder head. These are theoretical ideals that are modified by other factors such as an ECU that was tuned for given correlation between thermistor and cylinder head. Without changing the map, increasing conductivity can have a negative for some of us. Your design works better than OEM because you have reduced heat capacity, but you, and especially Dan, have decreased conductivity, which is less than ideal, but according to your detailed scientific analysis with neither a voltage, temperature, or emission reading, is beyond reproach. You claim reduction in spikes is the benefit, but the true benefit is that the air gap lowers the temperature reading so that the ECU does not overly lean the mixture. I am sure your design works fine for you and better than OEM. I have congratulated you for an excellent design. I just have trouble with your theory and explanation, and I see room for improvement. Also, I see why Greg's and Pete's solutions work, which is something you seem to fail to grasp. FORE!!!!! The problem with using thermal inertia as an ideal is that it refers to two properties, conductance and volumetric heat capacity that are counter beneficial as they both increase or both decrease. You, apparently, and Dan, certainly have decreased both conductivity and heat capacity and FWIW, also decreased thermal inertia. If you were to maintain the same conductivity between cylinder head and thermistor, and you decreased heat capacity of the sensor body and holder, we can say that thermal inertia was reduced, but it is the decreased heat capacity that was the benefit, because reduced thermal inertia is not necessarily a good thing. If you were decrease conductivity and maintain heat capacity, we would also have a decrease in thermal inertia, but I think WE all would agree that is the wrong way to go. What WE can't seem to agree on is that decreased heat capacity (surrounding the thermistor) and increased conductivity (from cylinder head to thermistor) is the theoretical ideal ( and the real world ideal, IF your bike does not run too lean due to the increased conductivity) What I liked about Velf's solution is that he decreased heat capacity, but he also decreased conductivity, which I question the wisdom of, but like you, he has seen benefits, so more power to him, to you, and to Dan, despite the fact that you have all decreased conductivity. It is pretty obvious that the positive effect of reduced heat capacity outweighs the reduced conductance. I suspect this is largely because the radiation of heat transmits enough to counter the losses due to the insulating qualities of the air. Also FWIW, Heat radiation does not fit into the thermal inertia equation, but is certainly a factor. To sum it up, kudos to you three for doing better than OEM, but the reason is simply reduced heat capacity, and saying that it is because of reduced thermal inertia is misleading. Clunk goes the ball into the 18th hole, in far fewer shots than the master baiter Ratchet, who is wading through the gator filled swamp water trying to find the last of the four balls he brought with him. One lead filled as we might recall, another with a radiator attached, and another wired with resistors. Doesn't the PGA have rules against such play?
-
I remember well. I believe that capping off the curve in the map at a lower temperature will eliminate the negative effect of these "spikes". As we have noted, some bikes, like yours, Ratchet's and mine respond with lean symptoms when conductivity is increased, while Greg Field's, Pete Roper's, their clients, and others respond very well to the increased conductivity. For them the spikes are not a problem, which leads me to speculate they may be running a bit too rich. Some of this variation between bikes may be because the maps and trim settings in the ECUs are not same and some of it is likely just manufacturing variation. When Ryland, others and I came up with a procedure for setting the TPS, we had a heck of time because of the variations. People would try our method, get bad results, and then get better results following more random procedures. I suspect the largest variation is in the trim setting. Most of us have no idea what our trim is set to. Even with my TuneBoy, I can't tell what the trim is set to. I would not be surprised if Moto International and Moto Moda bikes are set to a richer trim than yours, Ratchet's and mine. Unless everyone rushes out and buys VDSTS or Axeone, we will never know the trim settings. The early V11s had a temperature map that will likely aggravate the effects of temperature spikes. The later V11s seemed to "fix" that issue by capping off the compensation curve at a lower temperature. The MGS01 caps off the curve at a lower temperature than any V11. Not being a road legal bike, it's goal is to run well, not pass emissions, so it can do that. I'll be experimenting...
-
No John, I can't explain it, because it is not true. Low or high thermal inertia is not what would make sense. This fact is exactly why your theory is wrong. You allege that your design works well because of low thermal inertia. Your design has low conductivity and low heat capacity. Low thermal inertia is the product of low conductivity and low heat capacity. In one short sentence: We want high conductivity and low heat capacity because it allows the sensor to accurately follow the cylinder head temperature. But one short sentence is not enough. Not all Guzzis tune the same. Some run rich. Some run lean. As Dan suggested, going with Greg's high conductivity, high heat capacity design will work for rich bikes, and Dan and your low conductivity, low heat capacity design will work for lean bikes. But neither follow the theoretically ideal high conductivity and low heat capacity, which is not necessary, because either Greg's or yours and Dan's solution can be great improvements on the OEM configuration. Also simply following the axiom, We want high conductivity and low heat capacity because it allows the sensor to accurately follow the cylinder head temperature, does not guarantee better results because we still need to match up the ECU's fuel output with the needs of the engine. If we are getting more conductivity, the ECU MAY overly lean the mixture. AAYMMV As Dan suggested, "if your bike has typical lean issues at hot temps, then the air temp sensor is the way to go; if it runs rich, the brass & goo is the way." There is a third way to go, and that is to combine high conductivity and low heat capacity with ECU reprogramming.
-
Wiki asks everyone, you just have to listen. Of course if you listen to some people, you'll end up believing Ratchethack and the WSJ are more correct than the "tyrannical" "philistine" "group think" of wikipedia
-
Credible????? Reads like you are defining Specific Heat Capacity, not Thermal Inertia. I prefer wikipedia, but I still wonder why conductivity and heat capacity aren't inversely proportional. Perhaps Ratchet can go to wikipedia and post how square wheels should be part of the formula????? Here is how the allegedly non-credible Wikipedia defines Thermal Inertia: [quote )Thermal inertia Thermal inertia is a term commonly used by scientists and engineers modelling heat transfers and is a bulk material property related to thermal conductivity and volumetric heat capacity. For example, this material has a high thermal inertia, or thermal inertia plays an important role in this system, which means that dynamic effects are prevalent in a model, so that a steady-state calculation will yield inaccurate results. The term is a scientific analogy, and is not directly related to the mass-and-velocity term used in mechanics, where inertia is that which limits the acceleration of an object. In a similar way, thermal inertia is a measure of the thermal mass and the velocity of the thermal wave which controls the surface temperature of a material. In heat transfer, a higher value of the volumetric heat capacity means a longer time for the system to reach equilibrium. The thermal inertia of a material is defined as the square root of the product of the material's bulk thermal conductivity and volumetric heat capacity, where the latter is the product of density and specific heat capacity: See also Thermal effusivity SI units of thermal inertia are J m − 2 K − 1 s − 1 / 2 also occasionally referred to as Kieffers[2], or more rarely, tiu.[3] For planetary surface materials, thermal inertia is the key property controlling the diurnal and seasonal surface temperature variations and is typically dependent on the physical properties of near-surface geologic materials. In remote sensing applications, thermal inertia represents a complex combination of particle size, rock abundance, bedrock outcropping and the degree of induration. A rough approximation to thermal inertia is sometimes obtained from the amplitude of the diurnal temperature curve (i.e., maximum minus minimum surface temperature). The temperature of a material with low thermal inertia changes significantly during the day, while the temperature of a material with high thermal inertia does not change as drastically. Deriving and understanding the thermal inertia of the surface can help to recognize small-scale features of that surface. In conjunction with other data, thermal inertia can help to characterize surface materials and the geologic processes responsible for forming these materials.(/quote) http://en.wikipedia.org/wiki/Volumetric_heat_capacity
-
Welcome to the par-thai! "The thermal inertia of a material is defined as the square root of the product of the material's bulk thermal conductivity and volumetric heat capacity, where the latter is the product of density and specific heat capacity" http://en.wikipedia.org/wiki/Volumetric_heat_capacity So, according to the formula, high conductivity and high volumetric heat capacitiy results in more thermal inertia. Brass has fairly high conductivity and volumetric heat capacity, so its thermal inertia is high. Air has low conductivity and low volumetric heat capacity so its thermal inertia is low. But IMHO, thermal inertia is not what we want. We want high conductivity and low heat capacity, as long as the sensor does not get too hot. Many forum members have had success raising the conductivity by adding thermal goo or other conductive material to the air gap, but some of us (Dan, Ratchet, myself, and others) found we would get lean running symptoms, because the sensor was getting too hot when conductivity was increased. Ratchet came up with an early solution of adding cooling fins to the sensor body to draw away the excessive heat. The counter argument was that it also reduced the non-excessive heat, and increased mass that needed heating. Dan and Ratchet then came up with the idea of using the air sensor to reduce the heat capacity of the sensor. A fine idea, accept it needs more air gap than the brass sensor in order to run cool enough. The air creates a delay, so it is not a perfect solution, but the reduced mass trumps the increased insulation, so it follows engine temperature better than the OEM configuration. Also, air allows for radiant energy to heat the sensor, so the air sensor with air gap responds to more than just thermal conduction. Ideally, we should have a low mass/ low heat capacity sensor with no air gap and the sensor not getting too hot. I'll be taking a different direction than Dan and Ratchet, by going with OEM sensor in brass housing with zero gap, and eliminating the too hot of a sensor issue by remapping the Engine Temperature Sensor table in the ECU using TuneBoy TuneEdit. Still it is not a perfect solution because of the mass and less than perfect conductance. I may trim the sensor down similar to what Velf did, to reduce the volumetric heat capacity, but then add a copper conduit to transmit the heat to the now shorter sensor tip, creating a faster path for the heat to pass between cylinder head and thermistor. Right now I am using copper conduit and the sensor is running just a little too hot. Once I remap it, I am confident it will run morer betterererer
-
IMHO Everyone seems to have an opinion about what the proper oil level should be. Dumping in 3.5 liters will get you to somebody's idea of proper level IMHO if you have the Pete Roper's Moto Moda shloppage sheet, you should run the oil between the high mark (dip stick screwed fully in) and the bottom of the sheet. I don't see why letting the oil drain for ten minutes when hot and changing your filter, then adding 3.5 liters won't get you there?!? Draining a cold engine for one minute in Winter might leave you overfilled. But keep in mind Pete's sheet lets you ride at a higher oil level. IMHO For me, before I had a sheet, keeping the oil level between two thirds full and full on the dipstick was ideal. I'd top it to the full mark and not let it drop below two thirds. Again opinions vary, and you want to base the setting on where oil consumption nearly stabilizes. For me it was at about 2/3. Others on the forum claimed no oil consumption at full mark with dipstick screwed out. So if that works for you, and your air box is not filling with oil, go with that! I added a modified version of Pete's sheet. My sheet rides lower than Pete's design, and I keep the level between the high mark and the plate that is higher than the high mark. Adding 3.5 liters gets it just about right for me with this setup, but I still pour in about 3.5 quarts, run it, measure dipstick, add oil, measure dipstick, add oil, until it measures right. IMHO there will be differing opinions.
-
Kudos! You got rid of most of the thermal inertia! I was wondering where they put that thermistor! Since Marelli has two models of varying length on the spec sheet, I figured it must be embedded higher up than some were suggesting. Our's probes in 27 mm while the optional one probes in 18mm. The thermistor must be about 12mm from the sensor body (27 - 15 = 12) How did you trim the brass without destroying the thermistor? Do you have X-ray vision, or were you just very patient? So, now you have over a 15mm air gap?
-
Yes two air sensors, good idea! Potentially much lower thermal inertia!!! Bravo! I don't have a problem with that, quite the contrary. But it is only a good idea if air gap is optimally set. Thermal inertia is nearly doubled if you double the gap, decreasing "accuracy". To reduce thermal inertia, the air gap should be set as tight as possible without the sensor becoming too hot. Ratchet wrote: To me, it seems that he found the ideal gap to be ~2 mm, but in this thread he suggested 5 mm is ideal. I assume the revision is the result of more research, or maybe he changed from measuring to the cage to measuring from the thermistor. Regardless, he has much less air gap than you. I sincerely think you would benefit by following his example. Why he does not challenge you on this is obvious. The counter argument to the suggestion that you narrow the gap, might be that you have already improved the thermal inertia issue so much over OEM that you don't really care if following Ratchet's recommendation would perform better. In the previous thread Ratchet posted the spec'd numbers for the GM sensor that you provided him, that were different than the Guzzi sensor. The GM sensor reads "hotter" which would necessitate more air gap than if you used GM rather than the Guzzi AIR sensor. The Guzzi oil and air sensors match not just closely, but identically. Why not use it instead?
-
If anyone is actually interested in using the Guzzi air sensor for this purpose, I was kind of joking about swapping the sensors, although I would not be surprised if it gave a better result. More likely, I think, using two air temperature sensors would be a better idea. (one to measure air temp at the airbox and one to measure cylinder head temperature) But the Guzzi air sensor is certainly more expensive than the GM air sensor, unless you get it second hand. In the other thread I posted a link to it being on eBay for a very low price. Earlier I thought an advantage of the Guzzi air sensor is that you might be able to bolt it down, rather than friction fit it like Ratchet did. But you showed that the GM can be threaded, so maybe that gives the GM sensor the edge?????? Still I prefer having the temp:ohms curve matching OEM brass sensor.
-
I won't move on because I am being helpful, correcting misleading statements of 5mm air gaps and suggesting the Guzzi air sensor that precisely matches the Ohm/temp curve of the "oil" temp sensor. Why not listen to different ideas?
-
Sorry, Bikez.com's 76HP is clearly wrong. Thanks for the correction I would have used wikipedia as a source, but I feared the wrath of the anti-wiki pro-wsj crowd. Wiki probably got there numbers from honda, which probably are crank HP, but still that would put RWHP well over 100HP and not 76HP. http://en.wikipedia.org/wiki/Honda_CB1000R In any case, the bike is a porker, unless you compare it to a 1970's Honda big four, and it is only slightly lighter than the alleged 218.0 kg (480.6 pounds) VFR. Add an equal weight rider and the V11 is comparable in torque to weight ratio to most naked sport bikes, but in HP to weight ratio, Guzzi loses...oh well. You can always do what Zebulon did.
-
So doesn't anyone wanna swap the "air temperature sensor" and the "'oil' Temperature sensor"? I swear the factory must have got them reversed. In the old thread three or four us all independently brought it up, but Dan and Ratchet seem to be ignoring the obvious. Do you guys have stock investments with GM?
-
I know it sacrilege to compare apples and oranges, but I guess that makes me a sinner. Can anyone guess what this bike is from Honda? Power: 76.43 HP (55.8 kW)) @ 10500 RPM Torque: 59.00 Nm (6.0 kgf-m or 43.5 ft.lbs) @ 8250 RPM Dry weight: 213.0 kg (469.6 pounds) Click here for answer Of course honda makes even less powerful porkers and more powerful street racers, like the CBR600RR that weighs wet what a GT1000 weighs dry, but then you are stuck with an engine with little low speed torque. If you want a Honda to be built to last like a Guzzi, you'd have to compare the Guzzi to a VFR, and then we get into the same weight category. The VFR (at least in its best years) wins on ease of ownership and HP, but the Guzzi wins on pleasure of ownership and low speed grunt. Weight is about the same. Fuel consumption is about the same. Durability is about the same(in VFRs better years)