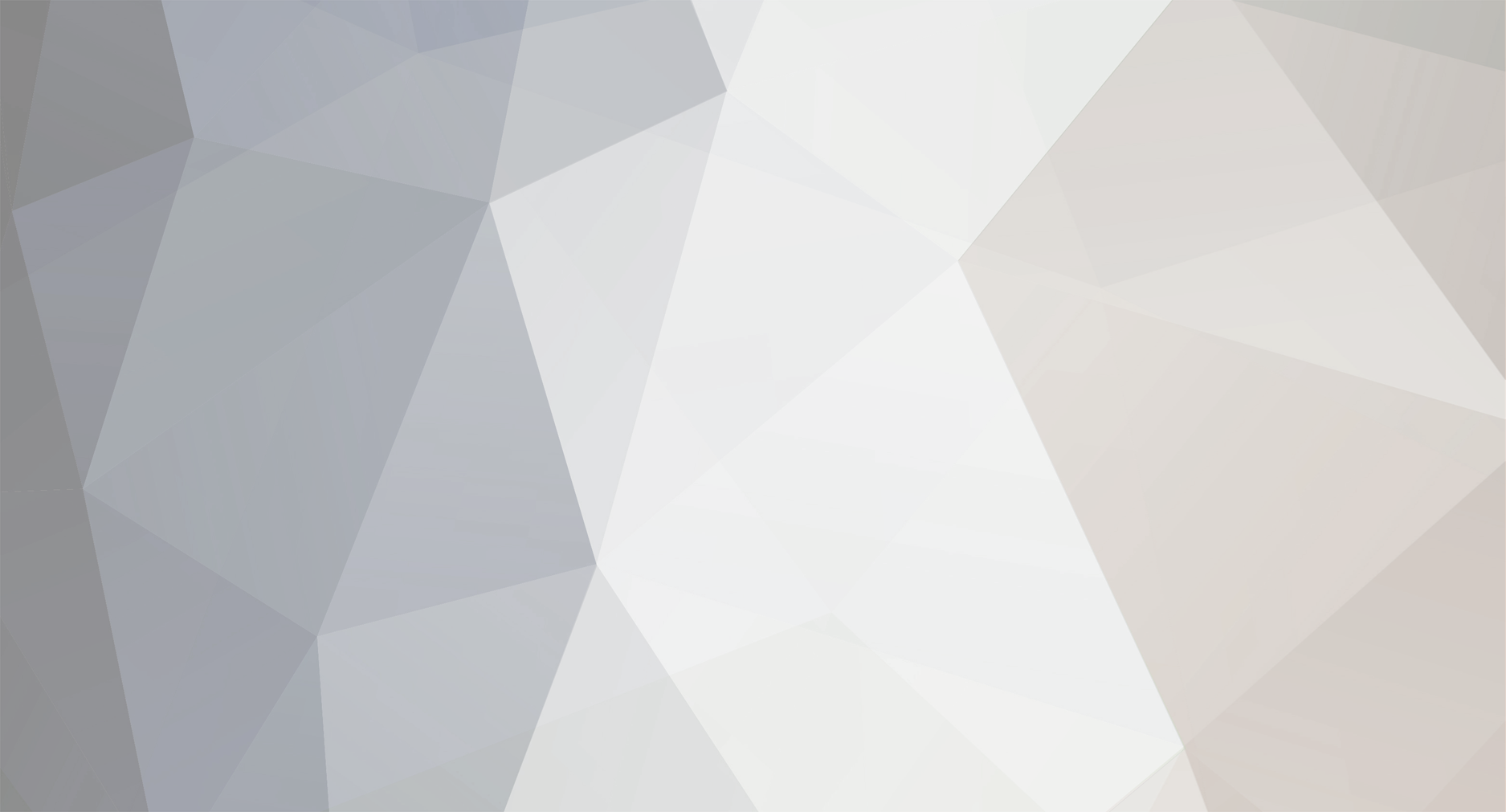
dlaing
Members-
Posts
7,096 -
Joined
-
Last visited
Content Type
Profiles
Forums
Events
Gallery
Community Map
Everything posted by dlaing
-
La Vache qui rit
dlaing replied to belfastguzzi's topic in Special place for banter and conversation
Listen here bodge master, I have not worn my hair like that in years! -
Right you are, here are some BST CF wheels with urethane bushings: Innovation often involves taking an idea that others huff at and making it sucessful. Greg Field is good at that. I am surprised he is not on board with urethane
-
Didn't someone once write something like that about multivalved engines and other innovations?
-
Radial brakes on upside down forks are more rigid and maintain better pad alignment. And disputably the bolts exhibit less shear force This results in real world differences for street bikes, but the differences may not be perceptable. There are certainly alot of sceptics out there. They probably have no benefit on up side up forks as the caliper brackets are normally shorter. I think in ten years 90% or more of new motorcycles with USD forks will move to radial calipers as there should be little increase in production cost. However as an aftermarket purchase, you won't get much bang for your buck by upgrading.
-
You can't have it both ways. The bolt is taking the primary force from only one angle. Describing it one way rather than the other does not allow the bolt to be withstanding two primary vectors of force. I am open to the possiblity that either of the bolt scenarios is at 90 degrees to the force, but not both. I am inclined to think the bolts facing the axle are taking the direct 90 degree force.
-
It is worth speculating about, because it is an important part of understanding physics and engineering design. I have been unsure about this one because it is complex. The force at one end of the caliper is different than the force at the other. Each bolt takes on different directional forces and yet they work together, supporting each other. Please answer this question: If the bolts pointed to the axle, would they be at 90° to the force?
-
No, they show a drawing of the caliper bolts going through a washer, the caliper and into the fork, but no part number. But the do give the part number for the washer!!!! 19 14 98 00 description: washer EDIT that was from the 2000 parts catalog. The 2003 shows the bolt: part number: 98 68 35 30 description: Screw
-
Guzzi sure messed up by not giving us color choices. Black may be fine for the Scuristas, but Swedish Gummy Fish Red would surely be more popular. (Sorry, your monitor may need calibration for color to appear correct) No pucking the pigglies permitted, puh-lease!
-
No surprise, Algor has the answer http://www.algor.com/news_pub/cust_app/queensu/default.asp Still, one needs to understand the physics in order to understand how to find the answer with the software.
-
Darn, you may be right. Each pair of piston's disk is being dragged along a different tangent. The average of the two is 90° to the bolts, but is that the force they are fighting? I need to think about this a bit.... EDIT OK, thought about it a bit and if you removed the lower bolt so that only the upper bolt remained, the upper bolt would not be a 90degree shear and likewise if you removed the upper bolt so that only the lower bolt remained, the lower bolt would not be under 90degree shear, but under more tensile force than upper bolt would be by itself. Do these forces balance out perfectly and create perfect 90 degree shear at each bolt? I am not shear sure
-
Just a part number: "98 23 08 20" and description: "screw"
-
Not a good answer, BAA, thanks for trying. Standard brakes' bolts are at a near perfect 90 degree angle. Radial brakes' bolts are slightly off from 90°. If the bolts were placed between the pistons in this image, they would be at 90° to the tangent, but the bolts are placed so that they are about 75° to the force.
-
I think it is a 485# spring which probably is fine for your weight. If it is that weight it should be marked with something like 1091 - 26/85 The 26 designates the spring rate of 485# If you give us some accurate sag measurements we could help you determine if the spring is the right rate, although the right rate is subjective.
-
Very interesting This is getting more and more intriguing. It makes sense that there should be some sort of damping to keep the cush from bouncing back and forth beyond the free play. Any force necessary to overcome the friction ain't gonna damage dah splines, but the friction may make drive lash more noticeable, and lubing a friction disk might make for less jolting drive lash, although possibly bouncier. To find out, I suppose you could temporarily reassemble without pucks to see if it provides friction damping. Or is the 'plate with gear' held up against the "gasket" by the pucks? I believe for it to function as a friction disk it cannot be clamped under the full force of the button screws, nor completely free moving. It would ideally have to be under some sort of fixed spring force, but there are no springs unless the washer or the pucks create the spring force. Since so many people have been lubing these for over 40 years, it is hard to believe it is a friction ring.
-
I have lots of low demand pipe dreams ideas! 1. rotating foot peg mount. Not a big change, but could be inexpensive solution. Ryland's are an awesome solution, and very reasonably priced, but I prefer going downward and rearward, but I think more people prefer to go forward like a tonti cruiser. The Buell solution certainly is not for everyone. Since the Buell footpeg solution, my foot has slipped off the rear brake a couple of times 2. Titanium rear sub-frame. (not much demand for that) (could work really nice with Paul M's rear cowling in carbon fiber ) 3. A kit to make bike look more like V7 Sport, with side covers saddle, metal rear fender(I think V7 was in Chrome, but aluminum would be nicer) Alpina spoked wheels would be the icing on the cake! 4. Carbon fiber airbox with ram air, and more filter element area. 5. Frame reinforcement kits. 6. A kit to rubber mount clip ons....I can here the peanut gallery groaning 7. Cush drive made of springs and oil dampers 8. Titanium axles. (My Ohlins equipped Guzzi can use Ducati front axle) 9. progressive shock linkage kit. 10. Longer swing arm (better for touring) 11+ etc.
-
Piddling may not be absolutely necessary, but I think it is a good idea, and FUN too! If you price is no object, get both direct link and motorbike diagnostics from techno research. TuneBoy MIGHT be cheaper, but is only in endless purgatory beta, I use it and it is great! Power Commanders are easier and will satisfy all but the most obsessed or demanding. Running the TPS a little high might be enough, and won't cost money. Stucchi crossovers, that Jason mentioned, are one of the best bangs for the buck for mid-range power....don't know why I don't have one? I guess it is because I keep waiting for a QuatD with stereo outlets. The Open Airbox mod is the cheapest bang for the buck, and it will give you a real raw sound that will suck the eardrums away from your brain.
-
What might be easy to build is a mount for the peg mount that rotates. Kind of like the Centauro peg, but less drastic, like maybe an adjustable 20-30mm change, so you could make it work with the stock foot controls. Stock foot peg including mount could be retained, or upgraded to a nice generic billet alternative.
-
So, Joe's Buell pegs arrived. Installation was a piece of cake. My Immediate impression after two one mile rides are that it is much more comfortable! My knees feel more relaxed, I feel like I have more control of the bike and the right foot is no longer annoyed by the brake master. All from an inch move Traction feels slightly better. My size elevens (US) had no problem reaching controls. Controls of course had to be lowered and that took some time to get right. Rear brake was easy and I like how I now have to reach in a little to activate it. The gear shifts are now done a little further out on the toe while before they were done at the foot where my toe begins...no problem, just different. Gear shifter is at its limit for how low it can go and not hit the pork chop. Some may find that too high, but it works well for me, especially when wearing large toed boots. I did not find them to be too far back, but I found that if I choose I can rotate the mounts, but I'll have to grind the lip down that prevents them from rotating more than a couple degrees. Thanks JoeV11! EDIT Here are some photos Brake Lever side http://img522.imageshack.us/img522/1861/buellpegrtk5.jpg Gear Shifter side http://img372.imageshack.us/img372/6182/buellpeglca1.jpg
-
Here is my highly controversial off the fairway, from planet Remulac, result of demon possession, yet nearly definitive guide to sag settings: Step 1 Drop the triple clamps down the forks 5-10mm from stock. WARNING make sure fender and tire won't collide with anything when bottoming out. Step 2 Measure sag with bike unladen and laden Get a competent assistant to measure. For laden sit in riding position with full gear on, and loaded with typical load (stuff like the clean underpants that Baldini mentioned). Fuel tank about 2/3 full. Be sure to take into account stiction by taking high and low readings at the respective stiction points and averaging out. RaceTech has a good article on how to do it. http://www.race-tech.com/articles/SuspensionAndSprings.htm Step 3 set sag to the following: If you can't get close by adjusting preload, you will need different springs. What is close enough is up to you. I believe the most critical number for determining if your spring rate is ideal, is the difference between unladen and laden sag. Some people on this forum target to 18mm unladen and 36mm laden for both the front and rear with a difference of 18mm. If you are within 5mm of those numbers, or better yet within 5mm of my numbers below, you should be in good shape. I target the following: REAR Sachs 10mm unladen 30mm laden (difference of 20mm) FRONT 20mm unladen 35mm laden (difference of 15mm) MODIFIERS (all are rough guesses or opinions...what is your's? ) *Racing, subtract 1 to 5 mm from laden sag. *Touring, add 1 to 5 mm to laden sag. *Frequent two up, subtract 1 to 6 mm from rear laden sag, and subtract about half of that from front sag. Note: this is assuming sag is measured without passenger. *Ohlins, add 5mm to rear laden sag. *Progressive springs, add 2mm to laden sag and subtract 1mm from unladen sag. *Short legs, add laden and unladen sag at a ratio of maybe 4mm additional laden for every 5mm additional unladen. (because shock needs to be firmer as travel decreases) *Rider weight greater than 80kg, add 1mm rear laden sag for each additional 20kg, and 1mm front laden sag for each additional 40kg *Rider weight less than 80kg, subtract 1mm rear laden sag for every 20kg less than 80kg and subtract 1mm front laden sag for every 40kg. *Personal preference, (no sag nazis here) add or subtract whatever you want to laden and or unladen sag numbers. This forum has 200#riders who have found 550# shock springs to be too stiff, and yet there are some like Dr.Know who might weigh 250# in full leathers, that that use 115N/mm or 657# spring. So everybody sure has there own taste in what works. Often trial and error is the best way to go, but the above info should help you get close so you won't have to try and error too many times. My numbers above are the result of a homogenization of opinions by experts and amateurs and some of my own limited experience and as you can tell they are rounded to the nearest 5mm. The 18/36mm numbers are a result of the 15/30 percent rule, also nice round numbers. Next year, after my fourth shock spring and third fork springs, I might modify them based on what works better for me SAA, YMMV.
-
How it moves it away from the controls is certainly one of my concerns. I am hoping I can rotate the peg mount five to ten degrees to bring it forward a little. Is that doable?
-
The only consideration I can think of is how to wipe the grin off you face that you will get. ...and make sure the sag is set up well. The firmness of the spring will mean it will need less preload, so you should have enough adjuster range to get the sag right, despite the spring being 10mm shorter. So don't worry!
-
Mike Wilson already cleared up the acceleration vs. deceleration so I don't know why you are going on about that. Regarding drilling's effect on driveline lash, I think it depends on how you define driveline lash. I define it as slack and cushion. Earlier I agreed I was WRONG about slack and freeplay. Of course slack is only increased when slack is increased. Lash is increased when slack and or cushion is increased but perception of lash is minimized when the cushion is optimized. Greg recommended drilling it as shown in the photo, because he said the pucks were too hard. I suggested urethane because it can be ordered in various hardnesses. And then I get attacked. WTF!?! Drilling holes in cush drives has only been done in V11s for a few years. As far as we know you are the longest going with such a drill job. It may last 40 years, but I don't know. I am not saying it is a bad idea, but the reaction I get as if I am calling you all idiots. I am the only one here whose cush drive rubbers ever failed, and they failed quickly. It is reasonable for me to have reservations about the drilling the cush drive rubbers. I think if urethane is too much trouble, than drilling is likely a good idea, but there have also been more than 40 years of Guzzi making cush rubbers without drilling holes in them. Are they so far off the mark that the rubbers have to be drilled as much as Greg did? Maybe, but I choose to be more conservative with my drilling, if I choose that path. And you say that is well off the fairway. But I say it is lined up just right for birdie. Drilling the heck out of it may be your perfect hole in one, or it may have rolled into the sand trap. But you may still finish better than par! It is difficult to see from here and I like to play within my ability. Trust, but Verify.
-
It seems like ideally the brake disks should interlock with the wheel rather than rely on friction grip. I wonder if the shear plane goes through the unthreaded shank of the bolts? I guess that would require the threads starting enough below the shear plane that the shoulder of the bolt could take the shear rather than the threaded part of the bolt. I suppose it could be re-engineered if Guzzi got it wrong, but at a compromise with the amount of threading. I guess radial brake calipers are designed to take some of the shearing forces away from the bolts.
-
A man is stranded on a desert island, all alone for ten years. One day, he sees a speck in the horizon. He thinks to himself, "It's not a ship." The speck gets a little closer and he thinks, "It's not a boat." The speck gets even closer and he thinks, "It's not a raft." Then, out of the surf comes this gorgeous blonde woman, wearing a wet suit and scuba gear. She comes up to the guy and she says, "How long has it been since you've had a cigarette?" "Ten years!" he says. She reaches over, unzips a waterproof pocket on her left sleeve and pulls out a pack of fresh cigarettes. He takes one, lights it, takes a long drag and says, "Man, oh man! Is that good!" Then she asks, "How long has it been since you've had a drink of whiskey?" He replies, "Ten years!" She reaches over, unzips her waterproof pocket on the right, pulls out a flask and gives it to him. He takes a long swig and says, "Wow, that's fantastic!" Then she starts unzipping this long zipper that runs down the front of her wet suit and she says to him, "And how long has it been since you've had some REAL fun?" And the man replies, "My God! Don't tell me you've got a motorcycle in there!"
-
Thanks Mike! I really appreciate your posts Comprehensible and no hostile attitude.